FACILITY ROOM
The facility room in a Semiconductor Manufacturing Plant houses essential support systems like HVAC (Heating, Ventilation, and Air Conditioning), power supply units, water treatment facilities, and gas distribution systems. It ensures stable environmental conditions and supplies necessary utilities to other floors.
Gas Compression
In semiconductor manufacturing, various gases such as nitrogen, oxygen, and hydrogen, are required at specific pressures for different processes. Gas compression systems are essential for increasing the pressure of these gases to meet operational requirements. Parker’s high-pressure fittings and valves ensure safe and reliable gas flow, while our advanced sealing technologies prevent leaks and maintain purity.
Transair Piping efficiently distributes compressed air or gas, ensuring consistent pressure and flow, crucial for semiconductor manufacturing precision. Parker’s High Pressure Hydrogen Hose handles high-pressure gases like hydrogen with exceptional durability and safety, ideal for critical gas compression applications. Push-in Fittings provide quick, secure, leak-free connections, maintaining gas supply integrity. Engineered Metal Seals prevent leaks, ensuring safe, efficient operation and gas purity.




Gas Purification
The purity of gases used in semiconductor processes is critical to prevent defects and ensure high-quality production. Gas purification systems are designed to purify gases to the ultra-high purity levels required for semiconductor processes. Parker’s precision fittings and valves handle ultra-pure gases without contamination, while high-integrity seals ensure that no contamination enters the gas stream. Advanced filtration systems remove impurities at the molecular level.




Bulk Chemical and Gas Distribution System
Semiconductor manufacturing requires the precise and efficient distribution of large volumes of chemicals and gases to various parts of the plant. Bulk distribution systems ensure these materials are delivered where needed, maintaining consistency and safety.
UHP (Ultra High Purity) gases are distributed through a complex pipeline system made from stainless steel, which ensures that the gases remain uncontaminated and at the required purity levels. The pipeline system includes components like UHP stainless steel fittings, pressure regulators, and valves to control gas flow and pressure precisely.
Chemical fluids are distributed via pipelines made from materials compatible with the specific chemicals being handled, such as PTFE or PFA. These pipelines are equipped with UHP valves and pressure regulators to ensure precise control over the flow and pressure of the chemicals, maintaining their purity and effectiveness.




Slurry Storage
Slurries, semi-liquid mixtures typically composed of fine solid particles suspended in a liquid, are used in chemical mechanical planarization (CMP) which is a critical process in semiconductor manufacturing. As slurries are abrasive, proper storage and handling is required to ensure their integrity and efficiency. Parker offers abrasion-resistant fluid conveyance solutions, including appropriate fittings and valves specified for the semiconductor industry.




HVAC
HEPA (High-Efficiency Particulate Air) and ULPA (Ultra-Low Penetration Air) filters are essential in HVAC systems for facility and sub-fabrication rooms in semiconductor manufacturing.
Products like Parker's MICROGUARD and MICROPLEAT filters provide high filtration efficiency, while LoadTECH® rigid cell filters and VARIFLOW® surface air filters ensure optimal airflow. DP® pleated filters enhance particle capture, maintaining a clean environment that minimizes defects in semiconductor products and boosts yield and reliability.




SUB-FABRICATION ROOM
The sub-fabrication room is located below the cleanroom. This area contains critical infrastructure such as pumps, exhaust systems, and chemical delivery systems. It supports the cleanroom operations by managing waste, providing chemical feeds, and maintaining pressure differentials to prevent contamination.
Water Deionization
Deionized (DI) water is essential in semiconductor manufacturing for cleaning and rinsing wafers. The purity of DI water directly impacts the quality of the semiconductor devices. The process of water deionization removes ions and impurities from water through ion exchange resins, producing high-purity DI water.
DI Water Polishing then further purifies DI water using advanced filtration and reverse osmosis to achieve ultra-high purity levels.
These applications require high-purity fittings and valves, such as UHP PFA Fittings from Parker, to prevent contamination and ensure smooth flow. Advanced sealing technologies are also essential to maintain purity and prevent leaks. Additionally, filtration technology, including the Clariflow®-E-SELECT Pleated Membrane Filter Cartridge, incorporates fine filters and UV sterilization to remove residual particles and microorganisms. The UHP Inline Static Mixer ensures consistent mixing while maintaining ultra-high purity.




Fluid Distribution
Fluid distribution systems deliver chemicals and slurries to different parts of the semiconductor fabrication process. Efficient and safe distribution of chemicals and slurries is critical for various processes in semiconductor manufacturing. Parker offers a wide range of ultra-high purity PFA and PTFE fittings, pressure regulators, and valves that allow precise flow control and fluid handling.
The Chemical Manifold Box (CMB) is a centralized unit that controls the safe distribution of high-purity chemicals from bulk storage to various points of use, typically cleaning, etching, deposition. The CMB provides precise control over the flow of chemicals to ensure that each process receives the correct chemical at the required flow rate and pressure. In this context, systems require corrosion-resistant fittings and valves to handle aggressive chemicals and abrasive slurries, as well as high-integrity seals, such as ULTRA™ perfluorinated elastomers (FFKM), to prevent leaks and contamination.




Gas Distribution
Gas distribution consists of delivering high-purity gases like nitrogen, oxygen, and hydrogen to different process areas. Precise control and safety measures are needed, and particularly in face of flammable gases.
The Valve Manifold Box (VMB) is a centralized unit that controls and distributes gases safely, reliably, and precisely to the points of use within the fabrication facility. The VMB acts as a hub for distributing gases from bulk storage or gas cabinets to various tools and processes within the fabrication area. Safety is paramount due to the potential hazards associated with high-purity and often toxic gases.
The Gas Cabinet securely stores gas cylinders, ensuring they are kept in a controlled environment to minimize risks associated with hazardous materials. Parker’s ultra-high-purity stainless steel fittings, pressure regulators, flow controllers and diaphragm valves ensure precise and consistent delivery of gases at the required specifications.



Piping System
Specialized piping systems are the backbone of the sub-fabrication room, facilitating the transport of gases, chemicals, slurries, and DI water throughout the Semiconductor Manufacturing Plant. The network of pipes uses materials like stainless steel and specialized plastics for corrosion resistance and purity. It also includes inline filters that remove particles and impurities from fluids, and reliable seals to ensure leak-free operation and prevent contamination of the fluids and gases. Contact us for further information.


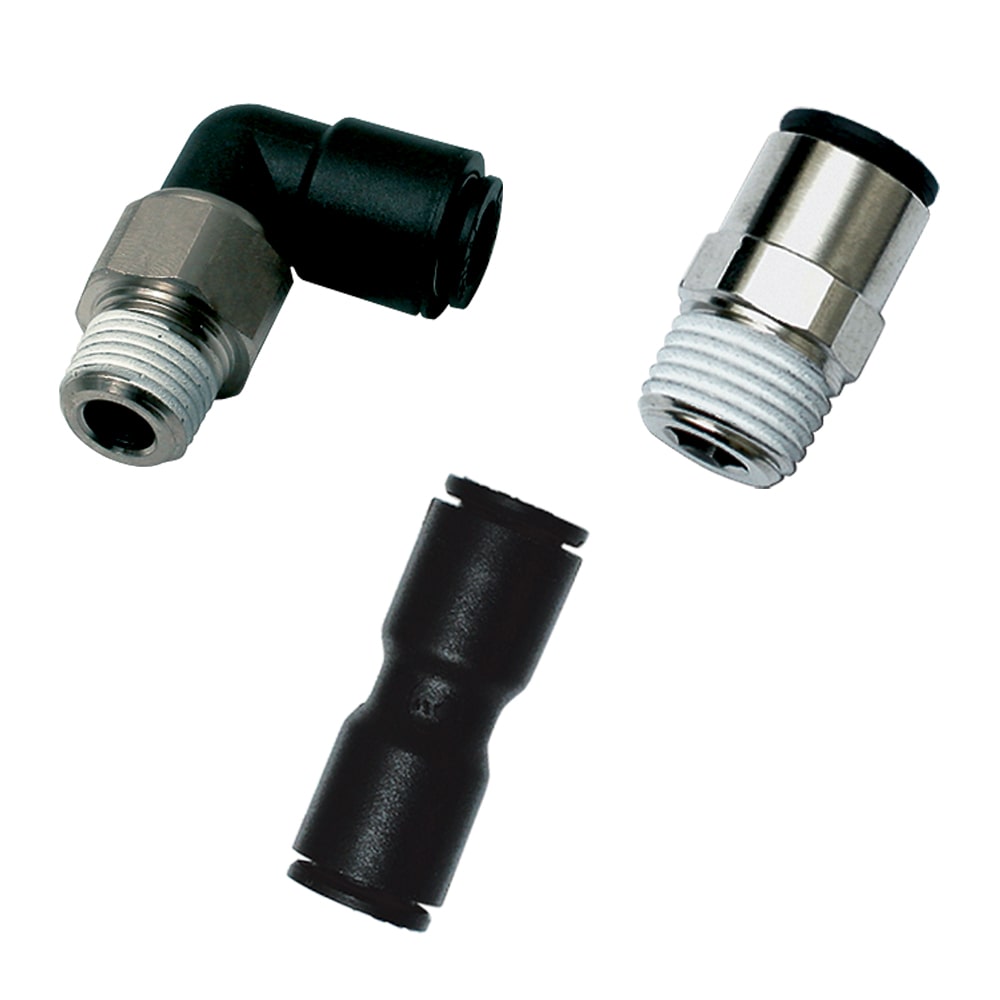

HVAC
HEPA (High-Efficiency Particulate Air) and ULPA (Ultra-Low Penetration Air) filters are essential in HVAC systems for facility and sub-fabrication rooms in semiconductor manufacturing.
Products like Parker's MICROGUARD and MICROPLEAT filters provide high filtration efficiency, while LoadTECH® rigid cell filters and VARIFLOW® surface air filters ensure optimal airflow. DP® pleated filters enhance particle capture, maintaining a clean environment that minimizes defects in semiconductor products and boosts yield and reliability.




CLEANROOM
The cleanroom is the core of a Semiconductor Manufacturing Plant. This ultra-clean environment is where wafer and microchip fabrication occur. It features stringent contamination controls, with filtered air systems and strict protocols to maintain low particle levels. The room is divided into different zones for photolithography, etching, doping, and other processes, ensuring precision and high yields in semiconductor production.
Fluid Distribution
Fluid distribution systems deliver chemicals, deionized water (DI water), and other process fluids to various tools and processes within the cleanroom. In the tool hook-up process, these fluids need to be delivered at precise flow rates and pressures, hence the need for pumps and valves with precise control mechanisms ensure accurate fluid delivery. Materials used in fluid conveyance must resist corrosion from aggressive chemicals. Parker offers a wide range of fluid conveyance solutions made from materials like PFA (perfluoroalkoxy alkane) or PTFE (polytetrafluoroethylene). Additionally, contamination control is critical to ensure that fluids are free from particles and impurities causing defects in semiconductor devices.




Wet Benches
Wet benches are specialized workstations used in semiconductor cleanrooms for processing semiconductor wafers through various wet chemical processing steps such as etching, cleaning, and rinsing of semiconductor wafers. They must ensure uniform chemical exposure to all wafers, as well as safe and precise handling of corrosive and hazardous chemicals. Parker offers an extensive range of corrosion resistant PFA or PTFE valves, pressure regulators and fittings, as well as PFA spray guns to streamline the process. Additionally, the Evolve™ Semiconductor Seal Ring provides high-purity, chemically resistant sealing solutions essential for maintaining the integrity and efficiency of the wet bench operations.

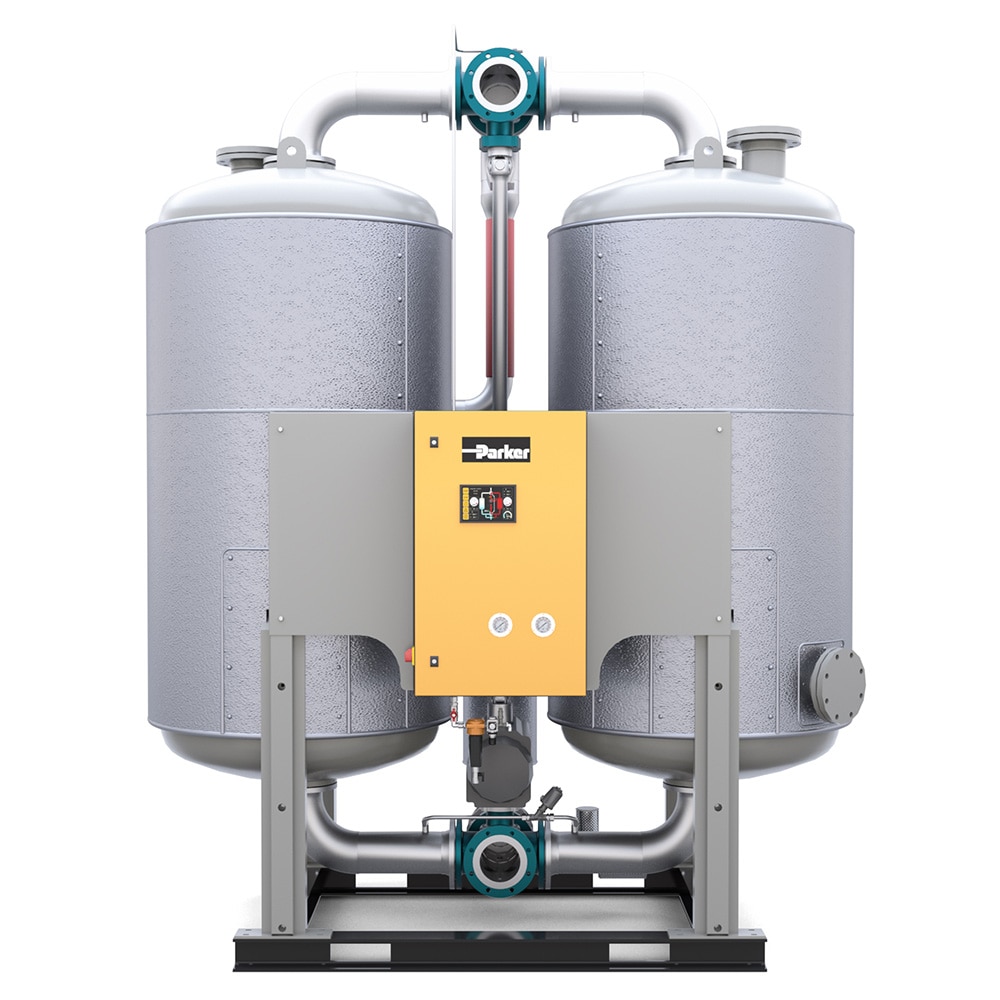


Thermal Management
Efficient cooling systems are necessary to manage the heat generated by semiconductor manufacturing equipment. Effective heat dissipation maintains optimal equipment performance. This application requires reliable and compact coolant distribution systems using materials compatible with the cooling fluids, which Parker can supply through its wide offering of thermal management fittings and couplings.




Valve Manifold Boxes (VMB)
Valve Manifold Boxes (VMB) control the distribution of process gases to various tools in the cleanroom. These applications are challenged to maintain gas purity, ensure leak prevention and allow flexibility to accommodate different gas types and flow requirements. Parker’s high-purity stainless steel fittings and metal seals ensure leak-tight connections.




Gas Cabinets
Gas cabinets store and distribute specialty gases used in semiconductor processes. As they are handling toxic, flammable, or corrosive gases, safety of the personnel and control of gas flow rates and pressures is vital.




HVAC System (High-purity)
In semiconductor manufacturing cleanrooms, maintaining stringent air quality is crucial. Parker's HEPA (High-Efficiency Particulate Air) Filters, specifically the MICROPLEAT series, effectively capture airborne particles, ensuring ultra-clean environments. Complementing these, the MICROPLEAT DM Ceiling Modules distribute filtered air uniformly, enhancing airflow efficiency and maintaining optimal conditions essential for sensitive processes.


FAN DECK
In the semiconductor industry, fan decks play a crucial role in maintaining the integrity of cleanroom environments, where the challenges of ensuring purity, precision, and reliability are particularly pronounced. These challenges include eliminating microscopic particle and chemical contamination, which can compromise wafer quality, and ensuring that fluid transport systems are both chemically compatible and free of impurities. Additionally, precise control of air and fluid flow rates is essential to maintain process consistency, while robust sealing solutions are required to prevent leaks and withstand harsh operational conditions.
Parker addresses these specific challenges with a suite of specialized products. Our high-efficiency HEPA and ULPA filters, along with chemical filters, ensure the air remains contaminant-free. For fluid conveyance, Parflex and Pure-Fit lines offer high-purity tubing and fittings, while our Veriflo valves and regulators provide the precise flow control necessary for semiconductor processes. Furthermore, Parker’s advanced sealing solutions, including both elastomer and metal seals, are designed to withstand the demanding environments of fan deck operations.




Roof HVAC System
In semiconductor manufacturing cleanrooms, maintaining stringent air quality is crucial. Parker's HEPA (High-Efficiency Particulate Air) Filters, specifically the MICROPLEAT series, effectively capture airborne particles, ensuring ultra-clean environments. Complementing these, the MICROPLEAT DM Ceiling Modules distribute filtered air uniformly, enhancing airflow efficiency and maintaining optimal conditions essential for sensitive processes.



