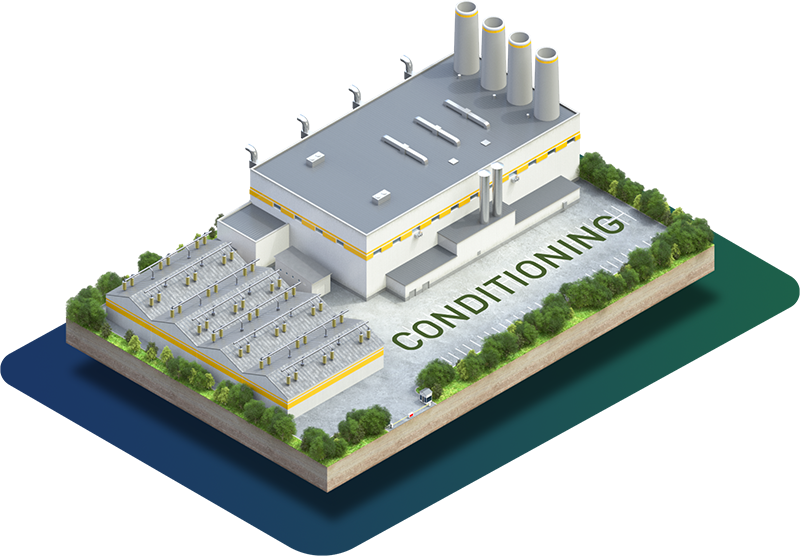
HYDROGEN CONDITIONING
Following production, hydrogen must be conditioned for practicality of storage and distribution. This is achieved by hydrogen compression or liquefaction.
Hydrogen compression
Hydrogen is typically produced at relatively low pressures (20–40 bar) and must be compressed prior to transport. Most compressors used today for gaseous hydrogen compression are either positive displacement compressors or centrifugal compressors. Positive displacement compressors can be reciprocating or rotary.
Hydrogen liquefaction
Hydrogen is commonly transported and delivered as a liquid when high-volume transport is needed in the absence of pipelines. Gaseous hydrogen is liquefied by cooling it to below −253°C (−423°F). Once hydrogen is liquefied it can be stored at the liquefaction plant in large, insulated tanks.
Solutions for hydrogen conditioning:
FLUID CONVEYANCE FOR COMPRESSION AND LIQUEFACTION
The use of fluid conveyance technology in hydrogen compression and liquefaction
Fluid conveyance products play an important role in hydrogen compression and liquefaction applications. Parker’s products are used to transport fluids such as hydrogen, which is a challenging fluid to transport due to its low density and high reactivity. In hydrogen compression and liquefaction applications, fluid conveyance products are used to transfer hydrogen gas from one location to another, control the flow of hydrogen gas, maintain system integrity and manage high-pressure conditions.
Featured fittings, connectors, regulators, valves, sensors and hose products
Fluid conveyance products are essential components of hydrogen compression and liquefaction systems, providing a means to transport and control hydrogen gas while maintaining system integrity and managing high-pressure conditions and Parker has a wealth of solutions to support the applications within this ecosystem.

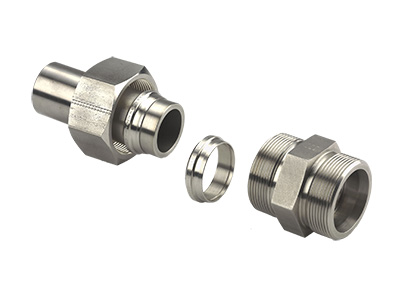
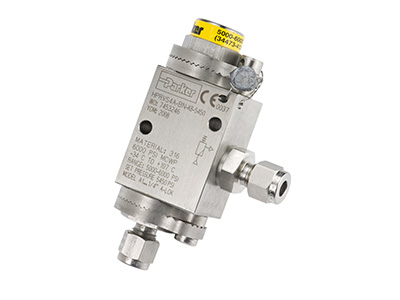
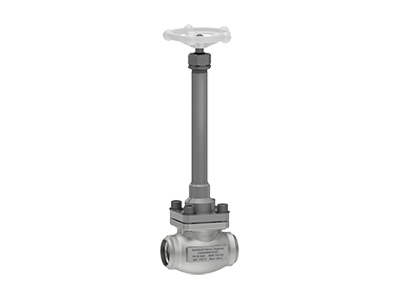
Related products:
- Seal-Lok™ Xtreme Tube Fittings
- EO Progressive Ring (DPR) System
- Two Ferrule Tube Fittings A-LOK®
- Single Ferrule Tube Fittings CPI™
- Medium Pressure Fittings Parker Autoclave
- Permanent Tube Fittings Phastite®
- Medium Pressure Needle Valves 20SM Series Parker Autoclave
- MPI Needle Valves MAN Series
- Medium Pressure Check Valves Parker Autoclave
- Globe Valves – Bestobell
- Lift Check Valves – Bestobell
- Safety Relief Valves - Bestobell
- Pneumatically Actuated Globe Valves - Bestobell
- Proportional Relief Valves HPRV Series
- Pressure Regulators IR4000 Series
- Modular Sample Conditioning System IntraFlow™
- Isolation Ball Valves Hi-Pro Series
- Ball Valves B Series
- Ball Valves, Trunnion Style, HB Series
HEAT EXCHANGE FOR COMPRESSION AND LIQUEFACTION
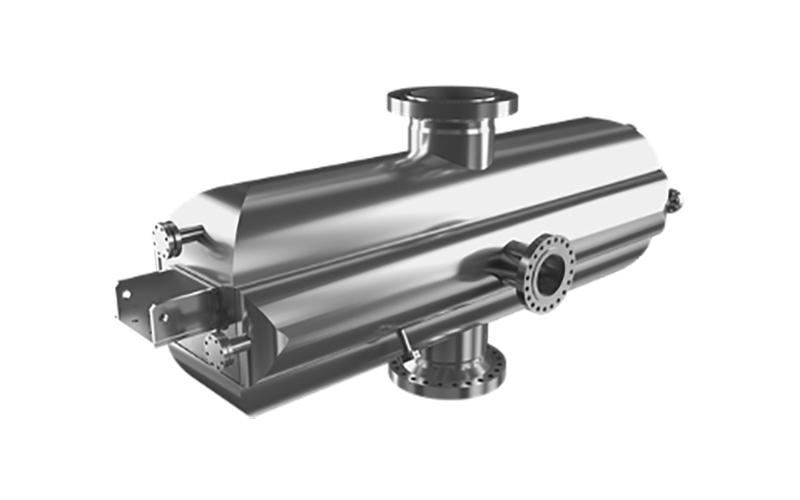
Parker’s Heatric Printed Circuit Heat Exchangers (PCHEs) are a compact, high-performance and bespoke solution optimized for hydrogen processing and conditioning. Up to 85% smaller and lighter than traditional heat transfer technologies, with multi-stream capability, the Heatric PCHE minimizes footprint and pipework complexity through compact engineering and design
Heatric PCHEs are manufactured using a specialized solid-state joining process known as ‘diffusion-bonding’. This process creates a heat exchanger core with no joints, welds, or points of failure. The resulting unit combines exceptional strength and integrity with high efficiency and thermal performance - to enable modern energy applications.”
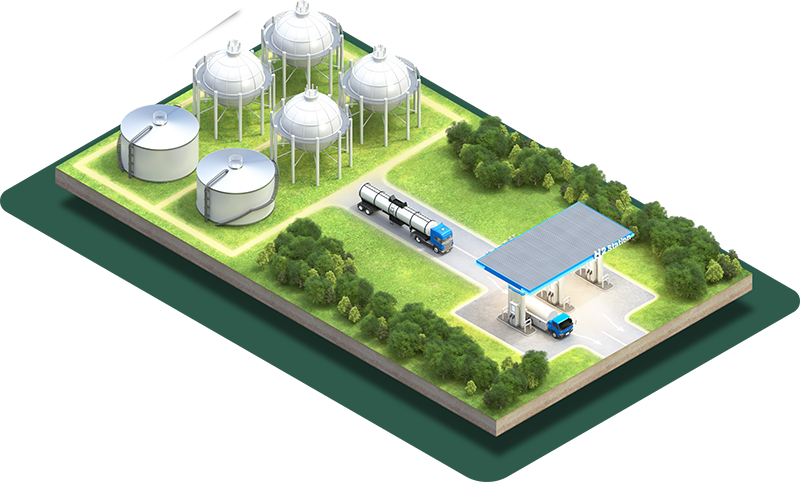
HYDROGEN STORAGE AND DISTRIBUTION
Due to its very low density in ambient conditions, the storage and distribution of hydrogen for use can be challenging. Hydrogen can be stored as a gas or liquid after compression and/or liquefaction.
Solutions for hydrogen storage and distribution:
SEALING TECHNOLOGY FOR GASEOUS HYDROGEN STORAGE
The use of sealing technology in high-pressure tanks for storing gaseous hydrogen
Gaseous hydrogen can be compressed and stored under high pressure of up to 700 bar and more. Various types of compressors such as piston, cylinder, and diaphragm compressors for high pressures and screw-type compressors for lower pressure ranges are used, depending on volume and pressure requirements. Avoidance of contamination of the hydrogen, for instance by lubricants, requires sealing solutions with low friction and low wear in an environment with minimal lubricants.
Featured sealing solutions
Reliable sealing solutions resisting high pressures, explosive decompression, and high temperature fluctuations are required, irrespective of type and size of the storage tank. The materials used have to exhibit high mechanical strength in order to withstand the risk of gap extrusion in high-pressure conditions. At the same time, low permeation is important to minimize diffusion losses and to prevent the risk of explosive decompression of the material in the event of a sudden pressure drop.
Learn more about sealing solutions for hydrogen storage:
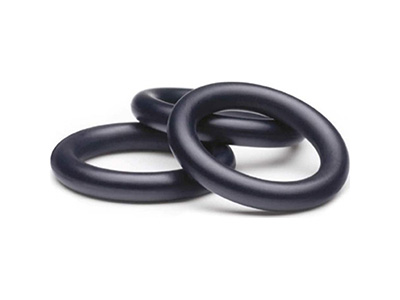
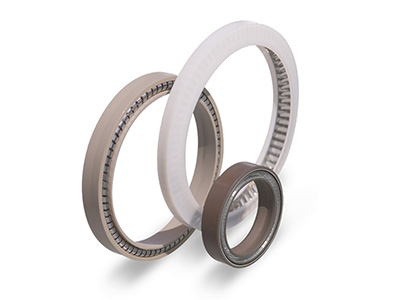
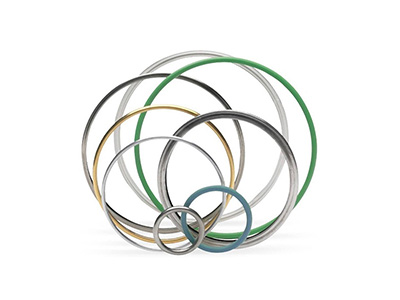
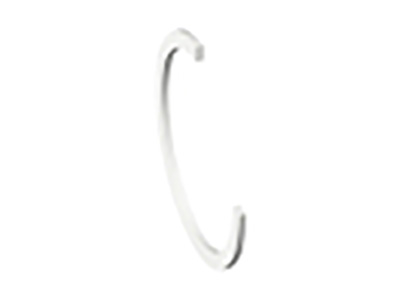
Related products:
SEALING TECHNOLOGY FOR LIQUID HYDROGEN STORAGE
The use of sealing technology in cryogenic tanks for storing liquid hydrogen
A cryogenic tank serves to store liquid hydrogen at -253 °C. Reliable sealing, for instance of the pressure and safety valves or the openings needed for filling or extracting hydrogen, is possible only with specialty sealing solutions. The same applies to sealing the entire line systems and related connectors and valves of the cryogenic tank system.
Featured sealing solutions
The cryogenic conditions prevent the use of classic elastomer seals. Solutions using specialty PTFE or metallic materials are preferably utilized instead. Combined with seal designs specifically developed for cryogenic conditions, these materials enable low-leakage solutions that are not prone to glass-hard embrittlement in cryogenic conditions. PTFE sealing solutions with steel springs (FlexiSeals®) or resilient metal sealing solutions are perfectly suited for sealing liquid hydrogen.
Learn more about sealing solutions for hydrogen storage:
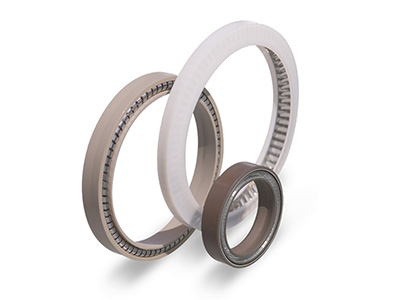
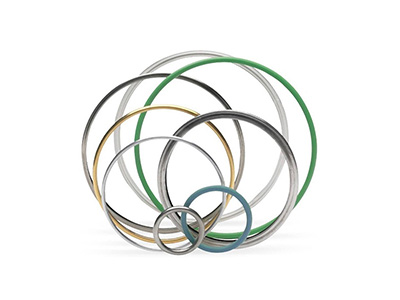
Related products:
SEALING TECHNOLOGY FOR HYDROGEN CARRIER STORAGE
The use of sealing technology for storing hydrogen by means of solid or liquid carriers
Hydrogen can be stored and transported by means of liquid carriers known as LOHC (liquid organic carriers) or solid carriers such as metal hydrides. For LOHC, similar to conventional fuels, the hydrogen can be handled by using existing infrastructure with sealing solutions made of LOHC-compatible materials. Sealing the solid carrier storage systems and their peripheries requires low-leakage sealing solutions to prevent potential safety risks due to hydrogen escaping from the storage system.
Featured sealing solutions
For both dynamic and static sealing of threaded connections, valves, housings, etc. of hydrogen storage systems, seals made of EPDM, butyl, or TPU materials meeting the exacting sealing requirements are available.
Learn more about sealing solutions for hydrogen storage:
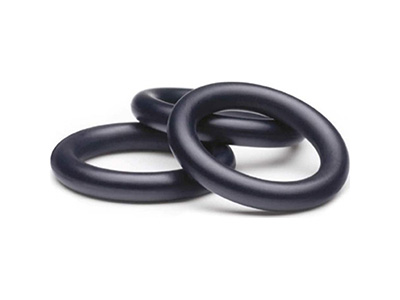
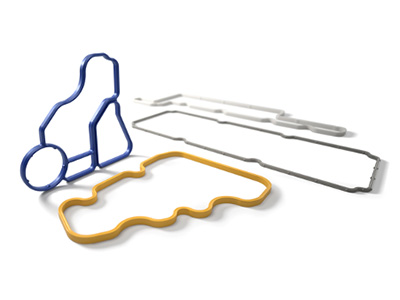
Related products:
FLUID CONVEYANCE FOR LIQUID HYDROGEN DISTRIBUTION
The use of fluid conveyance technology in hydrogen distribution
Parker’s Bestobell cryogenic valves are specifically designed to be used in cryogenic applications where extremely low temperatures are present. These valves are commonly used in the transportation of liquefied gases, including hydrogen, which must be kept at temperatures well below their boiling points to remain in their liquid form. When transporting hydrogen, the use of Bestobell cryogenic valves is important to ensure the safety and efficiency of the transport process. These valves are designed to withstand the extreme temperatures and pressures that are involved in transporting cryogenic fluids, such as liquid hydrogen.
Featured cryogenic valves
Parker’s Bestobell cryogenic valves are also designed to be highly reliable and to provide tight shut-off, ensuring that the hydrogen remains safely contained within the transport vessel. The use of cryogenic valves in the transport of hydrogen is important to ensure that the hydrogen is transported safely and efficiently, without the risk of leaks or other safety issues. These valves are an important component of any cryogenic transport system and can help to ensure the safe and reliable transport of hydrogen and other cryogenic fluids.
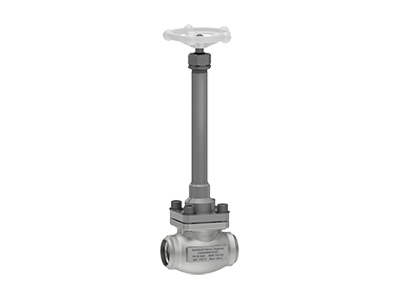
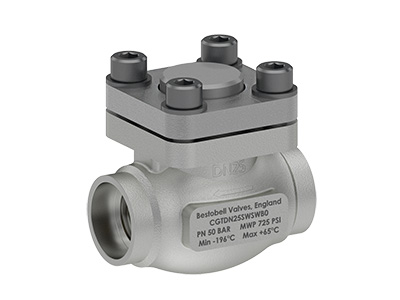
Related products:
- Globe Valves – Bestobell
- Lift Check Valves – Bestobell
- Pneumatically Actuated Globe Valves - Bestobell
SEALING TECHNOLOGY FOR HYDROGEN TRANSPORTATION
The use of sealing technology for transporting hydrogen on road/rail
Gases such as hydrogen are often hauled across long distances. In addition to pipelines and ships, routes on roads and railroads are frequently used. Parker Prädifa supplies reliable sealing solutions for the required ground transportation systems. Tailored sealing solutions contribute to safe transportation of hydrogen as a gas under high pressure or in liquid state at cryogenic temperatures.
Featured sealing solutions
In threaded connections and cover seals, O-rings and other static EPDM, butyl, or TPU seals are available specifically for these uses.
For sealing of liquid hydrogen, that is below -253 °C, specialty PTFE seals preloaded with steel springs (FlexiSeals®) or resilient metal seals (Enerings) such as C-rings are used.
Sensors ensure reliable monitoring of tanks and lines and can be sealed by means of static seals even at pressures above 700 bar.
Learn more about sealing solutions for hydrogen transportation:
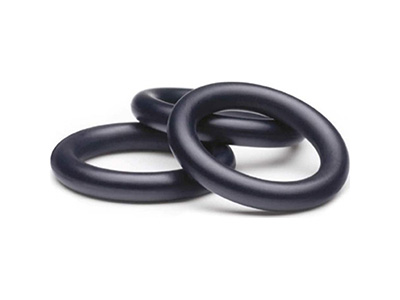
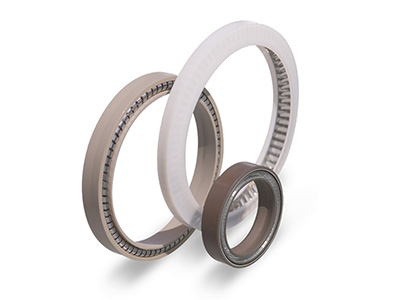
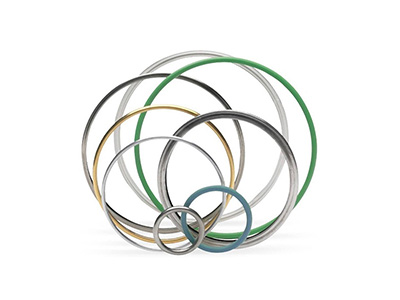
Related products:
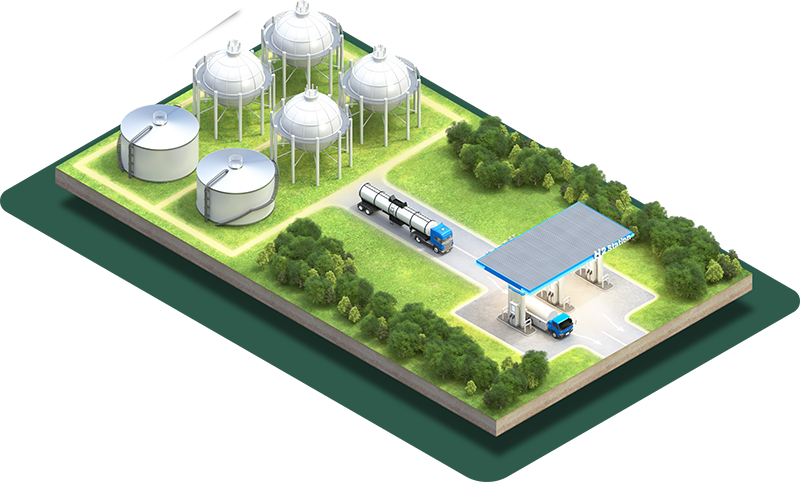
HYDROGEN DISPENSE
A hydrogen station is a storage or filling station for hydrogen. The hydrogen refuelling station (HRS) will boost hydrogen gas from various sources to pressures required in the transportation sector – either 350 barg (5,000 psi) or 700 barg (10,000 psi).
Solutions for hydrogen storage and distribution:
FLUID CONVEYANCE FOR HYDROGEN REFUELLING STATIONS
The use of fluid conveyance technology in hydrogen dispensing
Hydrogen dispensing stations use various small bore components to ensure efficient and safe refuelling of hydrogen to vehicles. Parker products are designed to withstand the pressure requirements of storage tanks and compressors to reach the required pressure of dispensing, which can be either 35 MPa or 70 MPa. The products are carefully engineered to provide the highest accuracy and repeatability, allowing for consistent performance and long-term reliability.
Featured fittings, connectors, valves, sensors and hose products
Parker’s fittings, connectors, hose and valves play an important role in hydrogen fuel dispensing systems and are designed to safely and efficiently transfer hydrogen gas from storage tanks to vehicles or other storage systems. Hydrogen is a highly flammable gas and requires specialized fittings, connectors, and valves to ensure that it is handled safely. These components are manufactured from materials that can withstand the high pressures and temperatures associated with hydrogen.

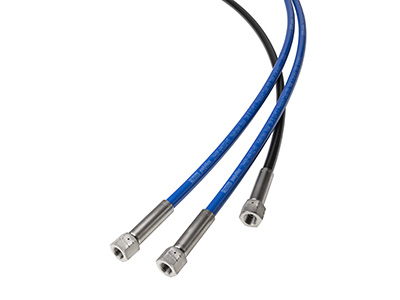
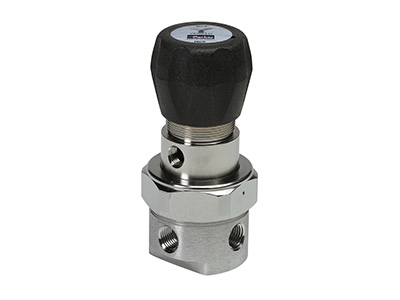
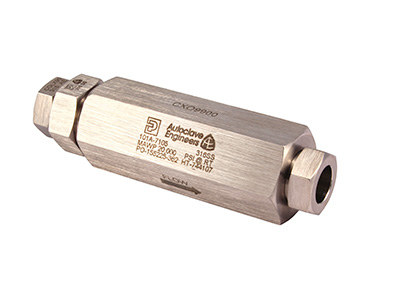
Related products:
- Seal-Lok™ Xtreme Tube Fittings
- Pressure Sensor SCP04
- High-Pressure Hydrogen Hose
- O-Lok® / Seal-Lok™ H22/H2P Tube Fittings
- EC-79 Two Ferrule Tube Fittings A-LOK® Series
- Single Ferrule Tube Fittings CPI™ Series
- Medium Pressure Check Valves Parker Autoclave
- Proportional Relief Valves HPRV Series
- Isolation Ball Valves Hi-Pro Series
- Ball Valves B Series
- Ball Valves, Trunnion Style, HB Series
HYDROGEN REFUELLING STATIONS SEALING
The use of sealing technology for dispensing hydrogen
In the filling process of vehicles and other consumers or of decentralized, stationary tanks, seals are exposed to significant pressure gradients. In combination with hydrogen’s high diffusion tendency, there is a risk of seal damage due to explosive decompression. The seals used for filling purposes must be resistant to mechanical stress and deliver reliable performance even at low temperatures.
Featured sealing solutions
For hydrogen systems, Parker Prädifa uses a special, intelligent seal design paired with low-permeation, mechanically robust low-temperature materials.
Learn more about hydrogen refuelling stations sealing:
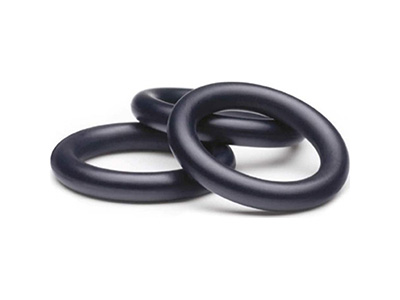
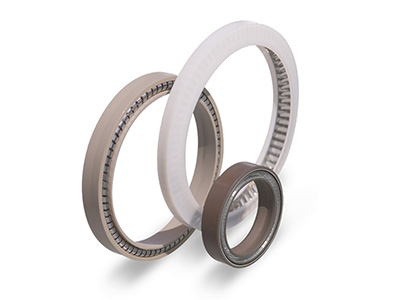
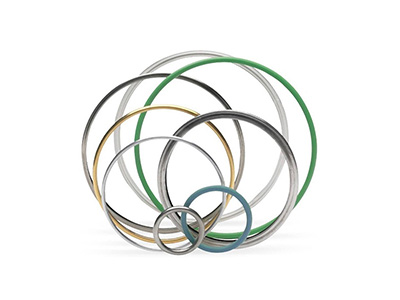
Related products:
HYDROGEN REFUELLING STATION (HRS) COOLING
Cooling within the HRS is critical to ensure the correct operation of the system and to cool the high pressure compressed gas to the correct temperature to enable hydrogen-powered cars to be refilled quickly.
Parker Hannifin can offer the following solutions for hydrogen refuelling station cooling:
HyperChill Process Chillers
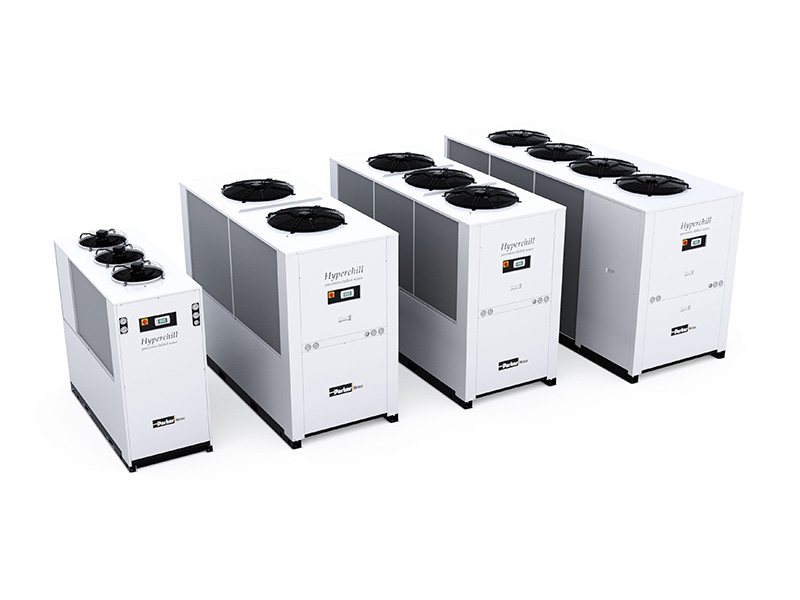
Extremely compact and easy to use, Hyperchill and Hyperchill Plus-E Chillers are designed for safe and reliable operation in various working conditions while providing a precise and accurate control of the process fluid temperature. The availability of a wide range of accessories and options makes Hyperchill and Hyperchill Plus-E a very flexible solution that fits the needs of all industrial applications
Related product:
Reference Materials:
Parker - Heatric Printed Circuit Heat Exchanger

Parker Hannifin’s Heatric Printed Circuit Heat Exchangers (PCHEs) are manufactured using a specialized solid-state joining process known as ‘diffusion-bonding’. This process creates a heat exchanger core with no joints, welds, or points of failure. The resulting unit combines exceptional strength and integrity with high efficiency and performance.
By incorporating diffusion bonding with micro-channel technology, Heatric can manufacture a unit that is up to 85% smaller and lighter than traditional technologies such as shell and tube heat exchangers. This reduction in unit size can lead to significant savings in structural costs due to elimination of excess pipework, frames, and associated equipment.
Related product:
Reference Materials:
HYDROGEN FILTRATION FOR FUEL DISPENSE
Hydrogen must be free of contamination for use with mobile applications to extend the life of sensitive fuel cell components. Filters at the refuelling station provide critical protection against contaminants before the gas enters the vehicle’s fuel tank. Multiple pressure and flow rate options allow flexibility with applications, up to 1000 bar and 300 g/s.
Features
- 316 Stainless Steel Construction
- SAE or Cone & Thread port types
- Pressure Ratings to 1000 Bar
- High Efficieny Particulate Filtration
- CRN in all provinces
- CE Marking in accordance with the Pressure Equipment Directive 2014/68/EU
Specifications
- Material: 316L SS
- Pressure Ratings: 700 bar or 1000 bar
- Flow rates: 120 g/s or 300 g/s
- Port: SAE and Cone & Thread options
- Material: 316L SS
- Pressure Ratings: 700 bar
- Flow rates: 60 g/s
- Port: SAE and Cone & Thread options