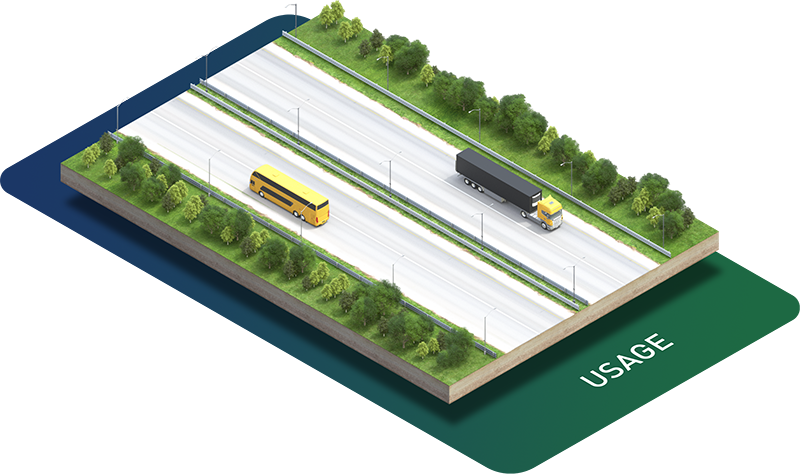
HYDROGEN FUEL CELL VEHICLE
The world is currently pursuing all possible means to reduce global warming emissions from carbon-producing fuels. Hydrogen plays a critical role in creating alternative systems that provide the carbon-free energy required for a sustainable future
The transportation market has accelerated its transition from fossil fuels towards zero emission, renewable fuels. In the “heavy” transportation segment where battery powered electric vehicles can’t fully accommodate the market, the fuel cell electric powertrain is an ideal solution.
The hydrogen fuel cell system
A proton exchange membrane fuel cell (PEMFC) system brings several challenges with it since it requires a high-level cleanliness for both the hydrogen and air streams. Parker can support OEMs in their development, with its wide range of products that will purify and condition the gases and liquids in the system, leading to a longer life and higher performance.
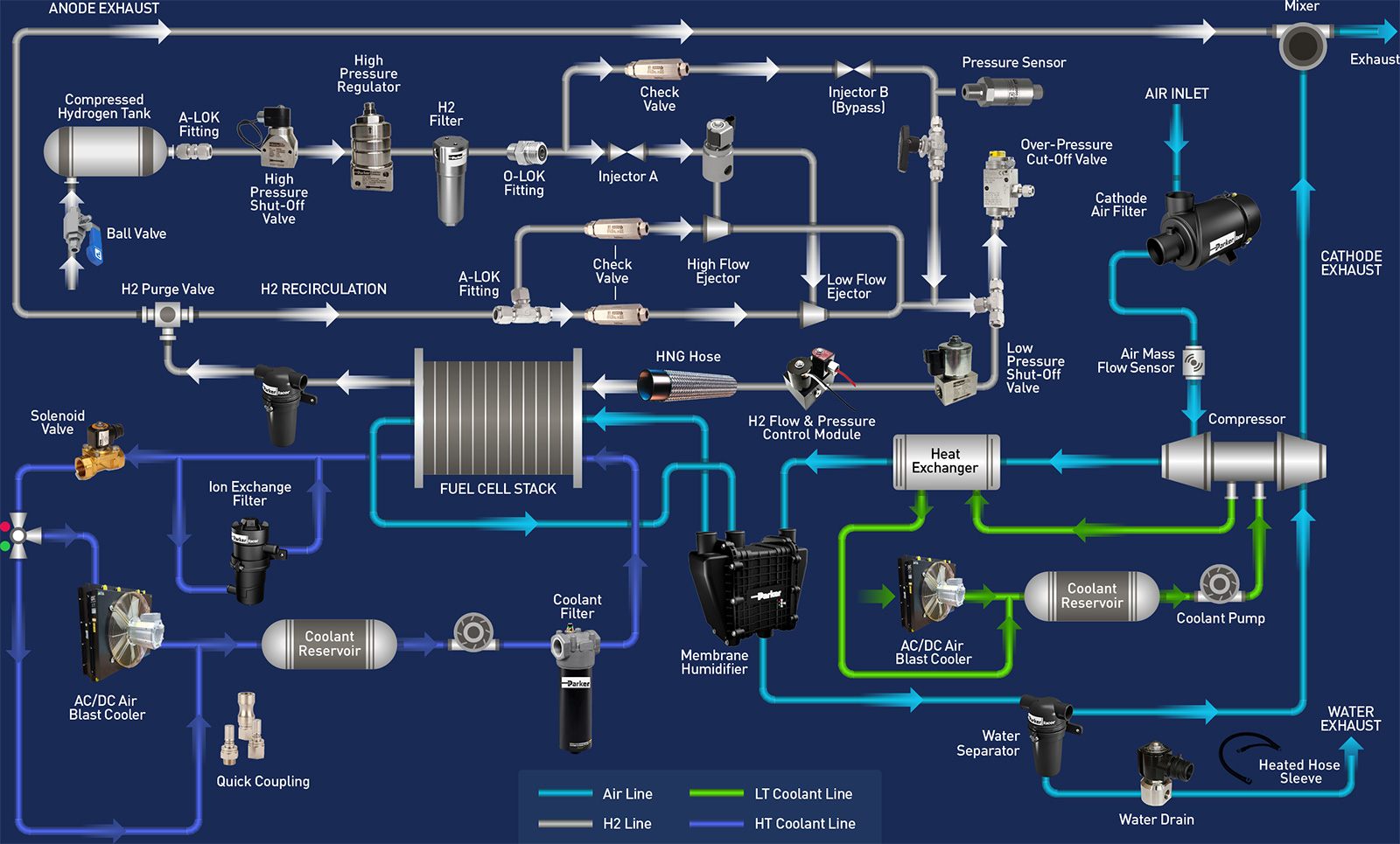
Solutions for hydrogen fuel cell:
- Ion exchange filters for hydrogen fuel cells
- Fuel cell stack cooling
- Cathode air filters for hydrogen fuel cells
- Humidifier for hydrogen fuel cells
- Cathode water separators for hydrogen fuel cells
- Anode water separators for hydrogen fuel cells
- Hydrogen filter for hydrogen fuel cells
- High pressure hydrogen valves for hydrogen fuel cells
- High pressure hydrogen regulators for hydrogen fuel cells
- Low pressure hydrogen valves for hydrogen fuel cells
- Hydrogen flow and pressure control modules for hydrogen fuel cells
- Fuel delivery to hydrogen fuel cells
- Fuel conveyance for hydrogen fuel tank systems
- Sealing technology for hydrogen fuel cells
ION EXCHANGE FILTERS FOR HYDROGEN FUEL CELLS
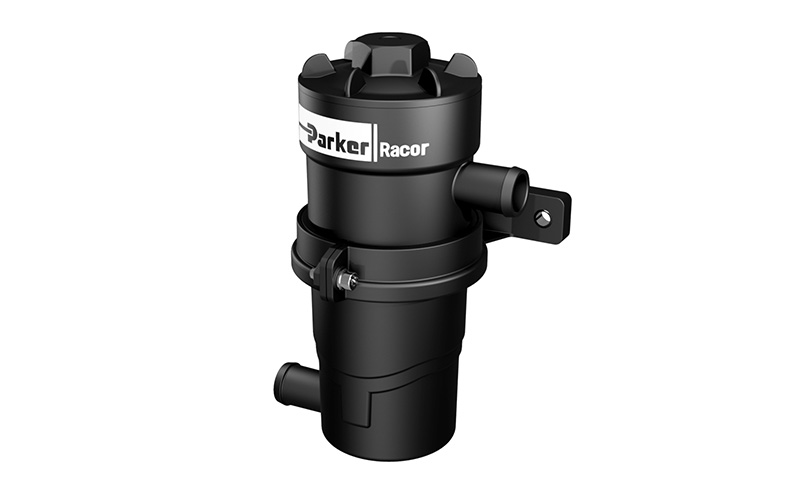
The fuell cell stack is sensitive to electric short circuits, therefore, the conductivity of the coolant needs to be controlled.
Parker Ion Exchange Filters reduce the conductivity level of coolant to optimal levels, protecting and extending the life of the fuel cell.
Features and benefits:
• Ion exchange beads developed for fuel cell applications
• Filter performance optimized to the application
• Flexible port and mounting positioning
• Replaceable service element
Specifications:
• Flow rate: 10 LPM
• Capacity: 100 meq (anion + cation)
• Electrical conductivity: >5 µs / cm
FUEL CELL STACK COOLING
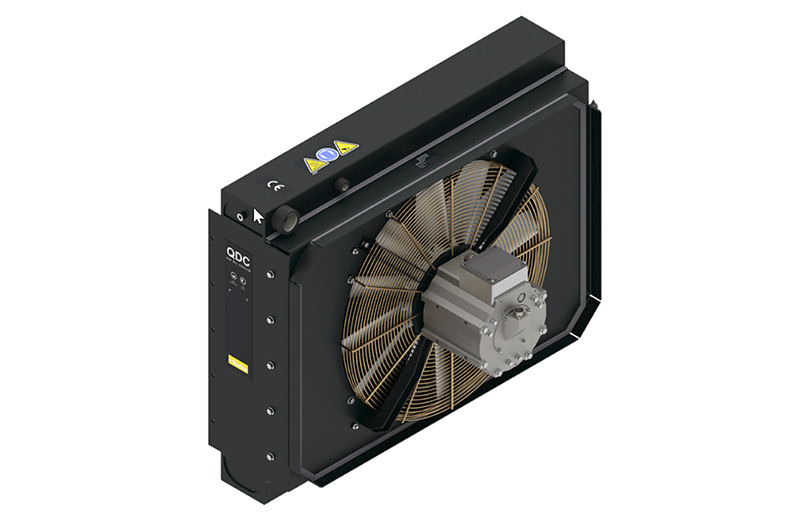
In fuel cell stacks coolers are used to maintain a stable operating temperature and prevent overheating of the fuel cell reaction, thereby maintaining a safe and stable operating temperature in a small tolerance field.
Parker’s QDC Quiet Air Oil Cooler with DC Motor and Quiet Air Fluid Cooler with AC or DC Motor remove excess heat from the fuel cell stack by circulating a coolant through a heat exchanger, which is in contact with the fuel cell stack. The coolant absorbs the excess heat and carries it away from the fuel cell stack, thereby maintaining a safe and stable operating temperature.
These coolers have the technical structure and the manufacturing process used (vacuum soldering) and subsequent rinsing of the parts in contact with the liquid increases reliability and reduces the risk of increased conductivity in the cooling liquid.
Related products:
CATHODE AIR FILTERS FOR HYDROGEN FUEL CELLS
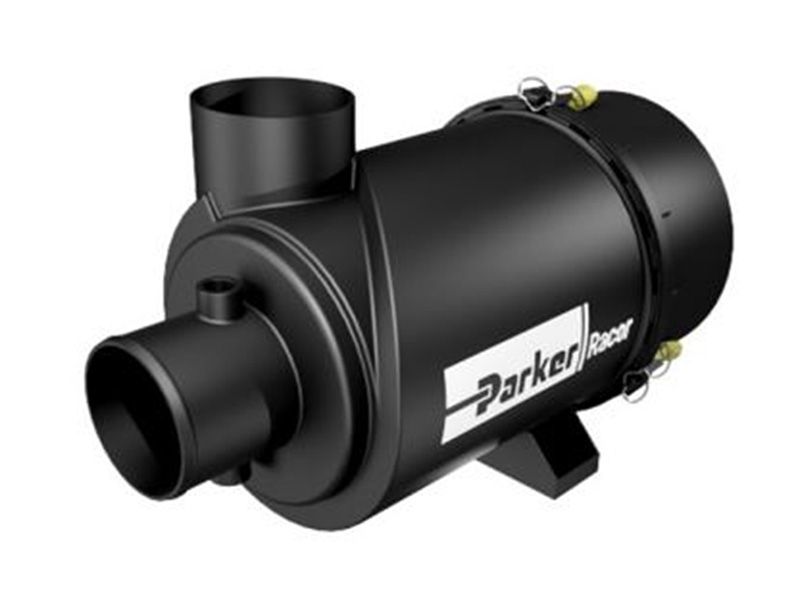
The fuel cell cathode is very sensitive to impurities and gasses that can choke and permanently deteriorate the fuel cell stack.
Parker Cathode Air Filters will remove particles and harmful gasses from the air stream protecting and extending the life of the fuel cell.
Features and benefits:
• Customized solution for your needs
• Global R&D media development and optimisation
Specifications:
• Flow rate: 2 – 6 m3 / min
• Particle removal: up to 99% @ 2.5 pm
• Gas removal: NOx, SOx, Ammonia
HUMIDIFIER FOR HYDROGEN FUEL CELLS
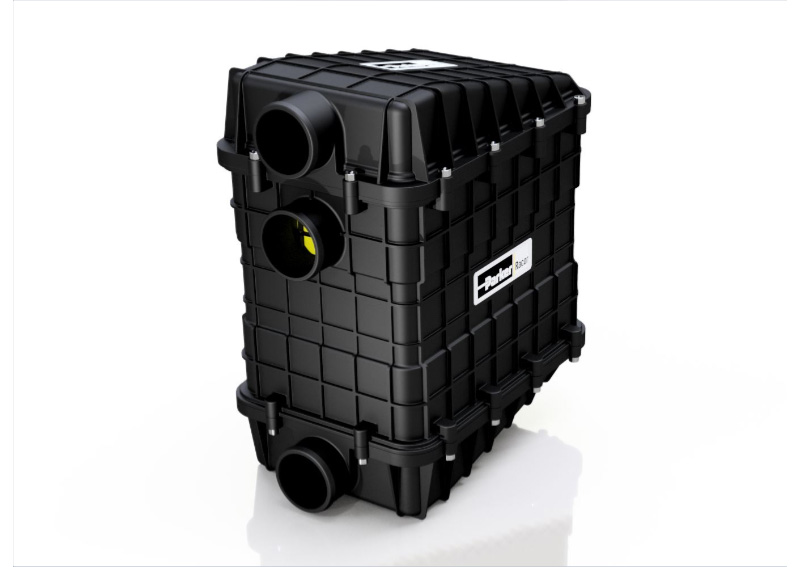
The proton exchange membrane needs to be kept humid to achieve maximum performance and extend the life of the fuel cell.
The Parker Humidifier will ensure the optimal level of humidity throughout the lifetime of the product.
Features and benefits:
• Proprietary technology delivers extended durability
• High resistance to chemical and thermal degradation
• Flexible port positioning
Specifications:
• Flow rate: 10,000 LPM
• Fluid temperature: -40 – 95°C
• Maximum pressure: 3 bar
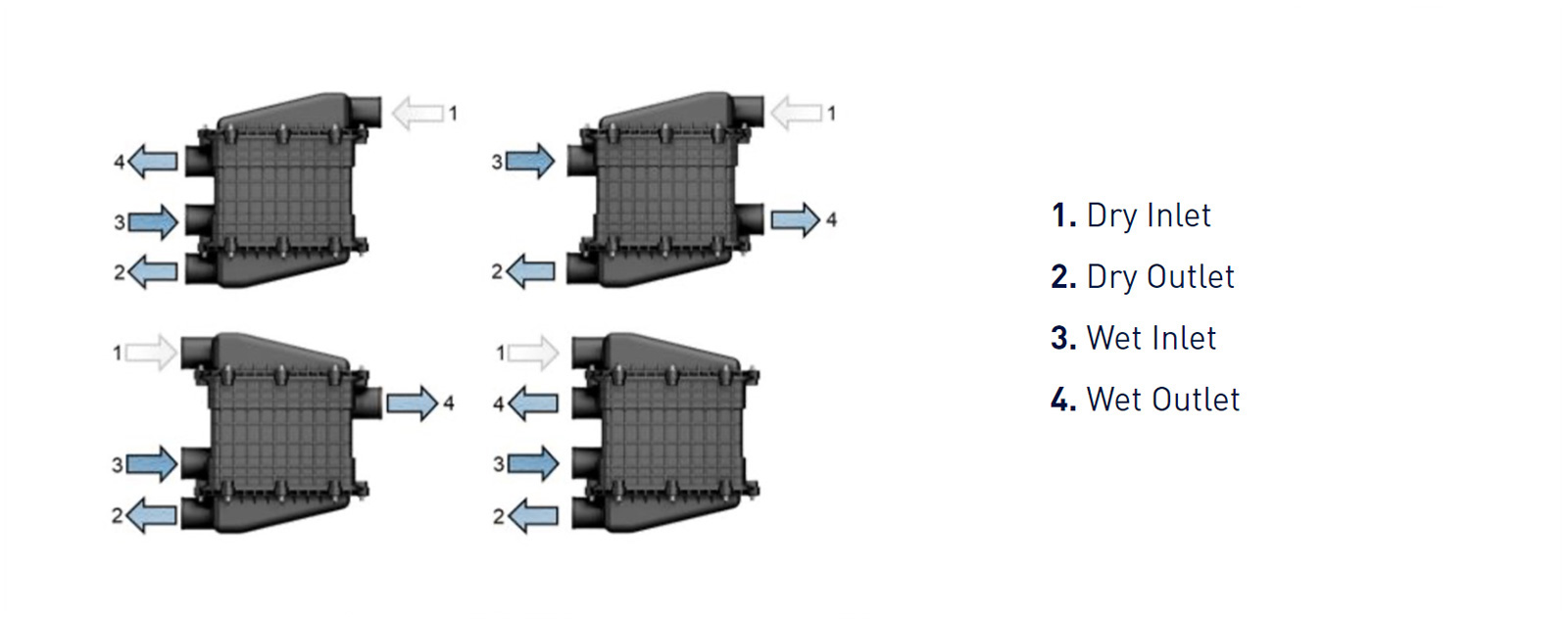
CATHODE WATER SEPARATORS FOR HYDROGEN FUEL CELLS
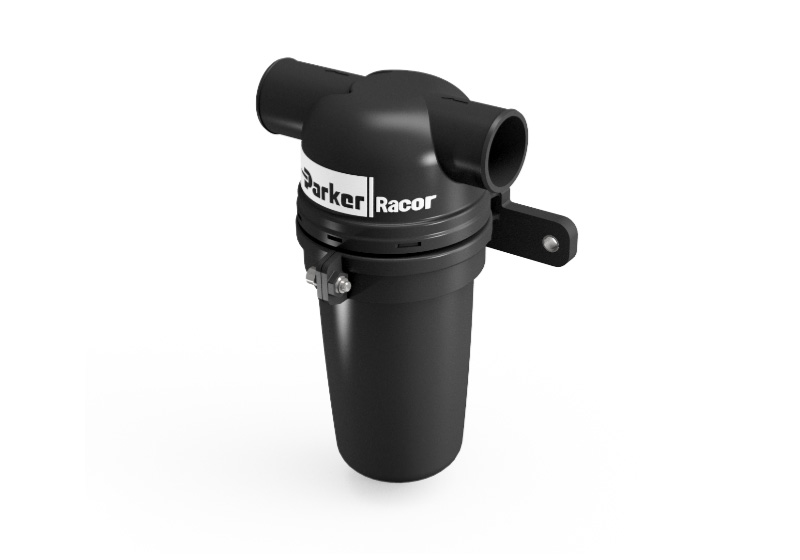
During operation the fuel cell generates a significant amount of water on both the air and hydrogen side that needs to be removed. The water generated on the cathode exhaust needs to be separated from the air to protect the compressor.
Parker Cathode Water Separator will remove the water from the air exhaust thus protecting the compressor and extending its life.
Features and benefits:
• High efficiency water separation
• Low pressure drop
• Mechanical separator with high durability
• Modular design for different flow rates
Specifications:
• Flow rate: 2,000 – 10,000 sLPM
• Fluid Temperature: -40°C – 95°C
• Efficiency: up to 99%
ANODE WATER SEPARATORS FOR HYDROGEN FUEL CELLS
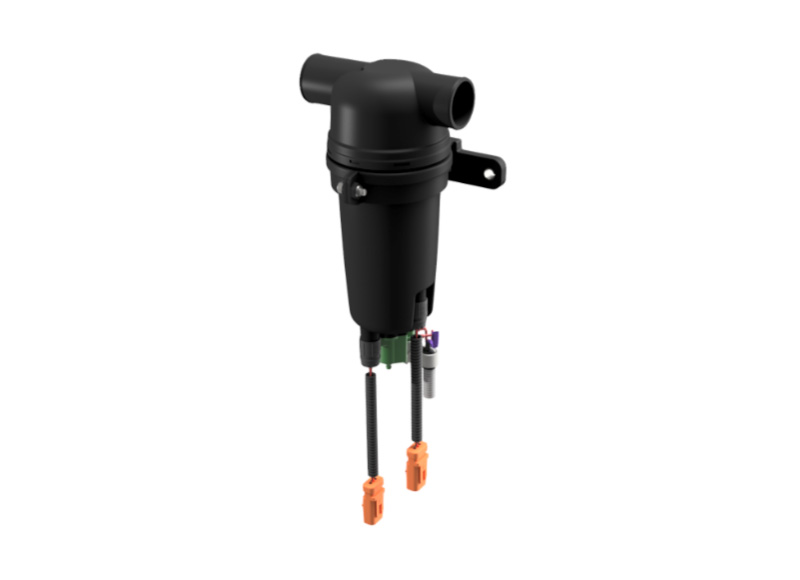
During operation the fuel cell generates a significant amount of water on both the air and hydrogen side that needs to be removed. The water generated on the anode side needs to be separated from the hydrogen return loop so that it is not recirculated into the fuel cell where it can flood the gas diffusion layer and negatively impact the performance of the stack.
Parker Anode Water Separator will remove the water from the hydrogen recirculation loop thus protecting the fuel cell and improving the performance.
Features and benefits:
• High efficiency water separation
• Low pressure drop
• Mechanical separator with high durability
• Modular design for different flow rates
Specifications:
• Flow rate: 1,000 – 5,000 sLPM
• Efficiency: up to 99%
• Automatic solenoid drain system
HYDROGEN FILTER FOR HYDROGEN FUEL CELLS
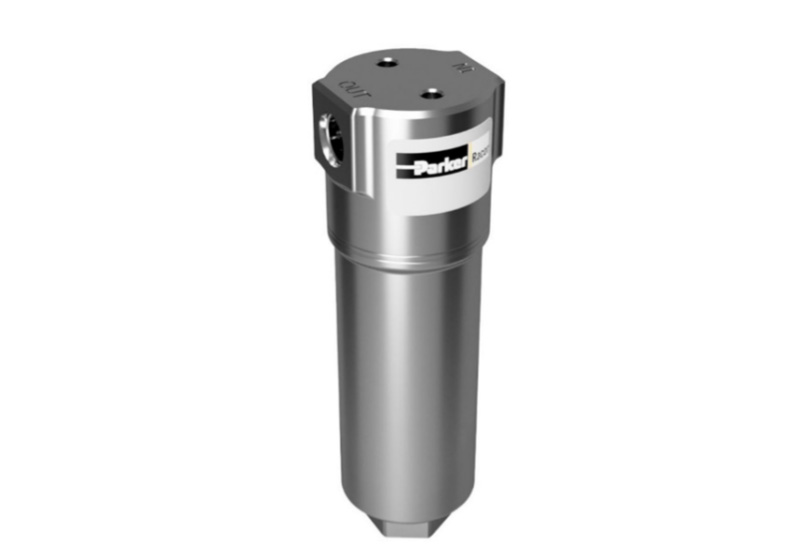
The fuel cell anode is very sensitive to impurities, thus a high-level purity hydrogen is required so as not to deteriorate the cell stack.
Parker H2 Filters remove particles and coalesce liquids from the H2 stream and can be used as a safety measure to protect the system.
Features and benefits:
• Coalescing and particle retention filtration
• Wide range of filtration types
Specifications:
• Filtration efficiency: 99% @ 3 microns
• Working pressure: Rated to 55 bar
• Material: Stainless steel
HIGH PRESSURE HYDROGEN VALVES
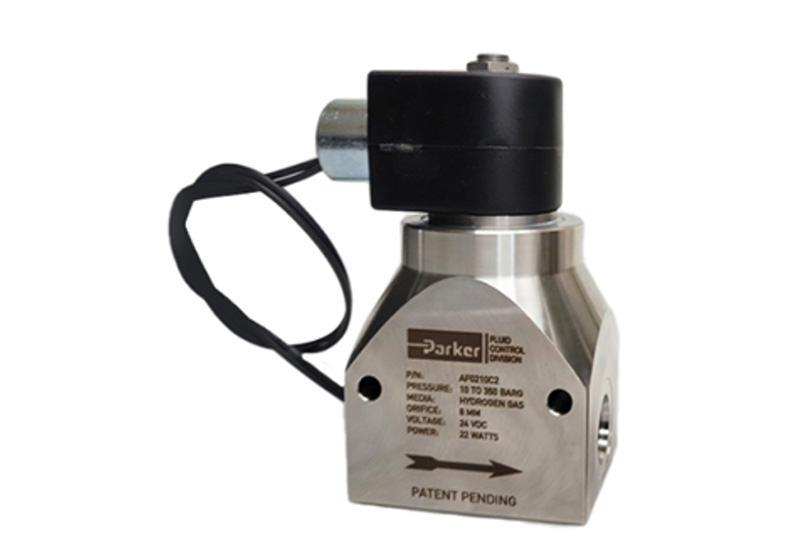
Designed for use in high pressure H2 systems up to 700 bar (10,000 psi), Parker’s hydrogen control valves allow the storage and use of hydrogen in fuel cell powered vehicles resulting in zero emissions.
Parker’s High Pressure Shut-Off Valve helps protect the fuel cell system from high tank pressures.
Features and benefits:
• Indirect pilot operated normally closed valve with precision orifice
• Stainless steel liner for additional stability against strain
• Wear compensating spring design
• Conduit sealing for protection in harsh environments
• High magnetic efficiency
• Redundant external seals
Specifications:
• Cv ~ 2.5
• Standard 22 watt fused Haz Loc coil
• 450G Peek construction for high pressure longevity
• Numerous connection options
HIGH PRESSURE HYDROGEN REGULATORS
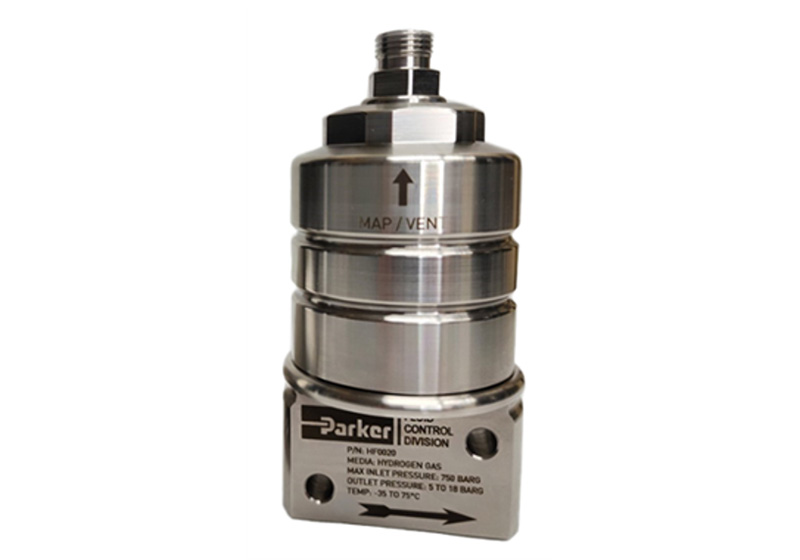
Designed for use in high pressure H2 systems up to 700 bar (10,000 psi), Parker’s hydrogen regulators allow the storage and use of hydrogen in fuel cell powered vehicles resulting in zero emissions.
Parker’s pressure reducing regulator controls H2 pressure levels for safe and efficient flow to the fuel cell stack.
Features and benefits:
• Heavy duty 316L stainless steel construction for harsh transportation applications
• Friction damped piston and poppet to reduce flow oscillation
• Pressure balanced poppet for reduced supply pressure effect
• Sealed bonnet and vent fitting for controlled external leakage
• Dome pressure bias capable (1:1) ratio for turbocharged ICE applications
• Low internal leakage (creep) design
• Wear resistant internals
Specifications:
• H2 compatible materials of construction
• Various outlet pressure levels available with tolerance ±1.0 bar at mass flowrate of 6 g/sec H2
• SAE J1926 o-ring and threaded cone & sleeve porting
• Multiple mounting options
LOW PRESSURE HYDROGEN VALVES
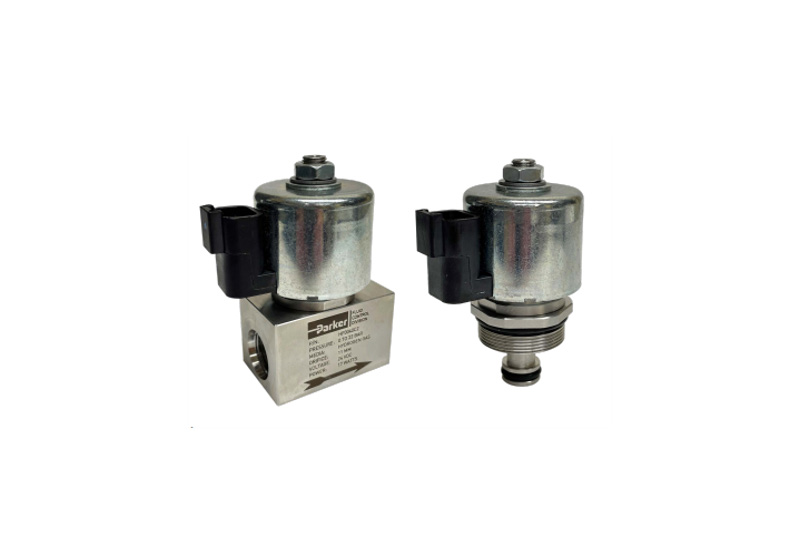
Designed for use in H2 systems, Parker’s hydrogen control valves allow the storage and use of hydrogen in fuel cell powered vehicles resulting in zero emissions.
Parker’s Low Pressure Shut-Off Valve helps allow proper control of hydrogen to the fuel cell stack.
Features and benefits:
• H2 material compatibility
• Optimized design to enable high flow coefficient in a compact size
• Different coils and connections available
• Cartridge version available for design flexibility
Specifications:
Valve function: 2/2 normally closed
• Maximum operating pressure: 22 barg
• Operating temperature: -40°C to +85°C
• Valve Body: 316L SS, Ports SAE J1926(-8, ¾-16 UNF)
• Orifice diameter: 0.43 in (11mm)
• Coil: 12VDC or 24VDC/17W, DT04-2P Deutsch connector, UL Class H(180C) Coil Encapsulation, IP69K moisture protection
• Internal seal material: HNBR / Buna-N
• Internal component materials: austenitic and ferritic stainless
H2 FLOW AND PRESSURE CONTROL MODULES
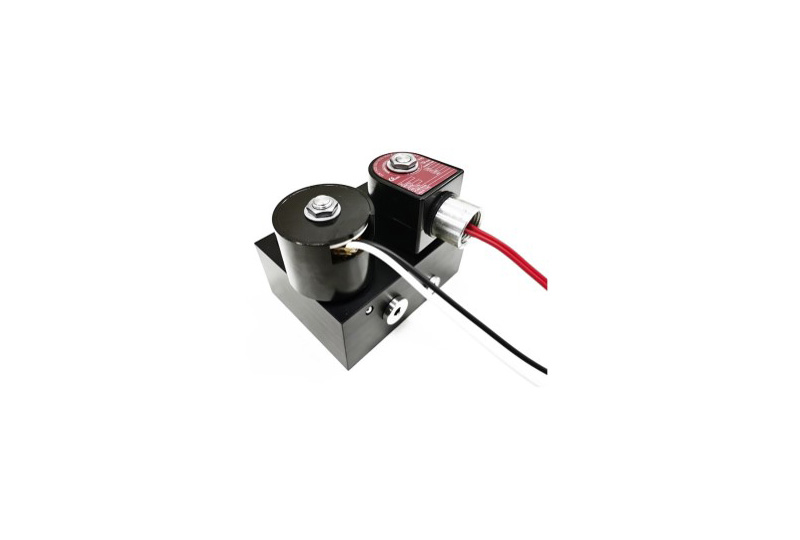
Designed for use in H2 systems, Parker’s hydrogen control modules allow the storage and use of hydrogen in fuel cell powered vehicles resulting in zero emissions.
Parker’s H2 flow & pressure module allows precise control of H2 to the fuel cell stack.
Features and benefits:
Integrated module with on-off, proportional, and exhaust control capabilities
• Less than 0.25 cc/min leakage at 20 barg
Specifications:
Aluminum body, HBNR seals, stainless steel components
• BSP standard connection with other options available
• Fluid temperature -40°C to 120 °C
• On-Off operating pressure 0-20 barg, orifice 8mm, working voltage 18-32VDC
• Proportional operating pressure 8-12 barg, orifice 3mm, flow 600L/min @12bar input, working voltage 20.5-32VDC
• Exhaust cracking pressure 1.9-2.1 barg, orifice 5mm
FUEL DELIVERY TO HYDROGEN FUEL CELLS
Heated hose sleeve solutions
Designed for heating media such as water to keep purge lines on fuel cells from freezing. Everthaw heated hose sleeves keep hoses flexible while keeping the fluid in the system free from condensation buildup.
Parker’s Compressed Natural Gas Hose is the only fully listed fluid conveyance system that is flexible. The flexibility of the product provides reduced warranty costs versus stainless steel tubing in vibration/movement applications. Constructed with an electrically conductive Nylon core to dissipate static build up and stainless steel reinforcement for corrosion and kink resistance.
Featured fittings
Parker supplies connectors for low-pressure systems that deliver hydrogen to the fuel cell. These products are compact and designed for leak-free media integration in fuel cell systems.
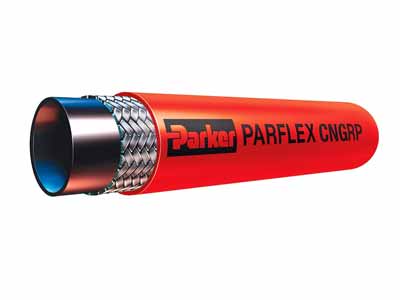
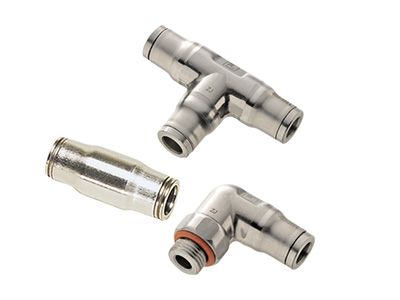
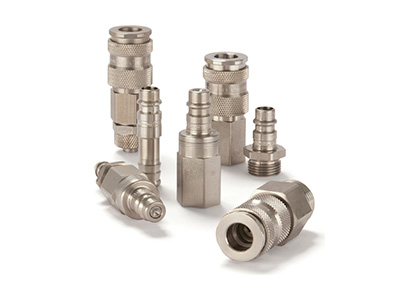
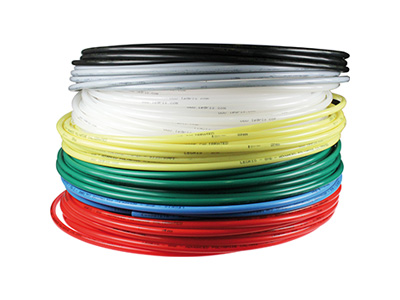
Related products:
FUEL CONVEYANCE FOR HYDROGEN FUEL TANK SYSTEMS
The use of fuel conveyance technology in hydrogen tank systems
Fuel conveyance products on hydrogen fuel tanks for trucks refer to the components that are used to store and transport Hydrogen fuel from the tank to the engine. Parker technology is used to connect, control the flow and to transfer hydrogen between different parts of the hydrogen fuel system, and are manufactured to meet the high pressure and extreme temperature requirements associated with hydrogen tank systems.
Featured fittings, connectors, regulators, valves, sensors and hose products
Parker can supply EC-79 fittings, valves, regulators, piping, pressure relief valves and sensors in a range of sizes, pressures, and temperatures. are critical, especially in demanding, corrosive, pressured and heat-intensive environments. All of these play a crucial role in ensuring the safe and efficient operation of hydrogen fuel cell vehicles. They are designed to be durable, reliable, and efficient, allowing hydrogen fuel cell trucks to operate with minimal downtime and maintenance.
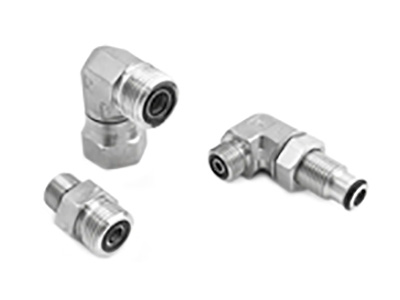
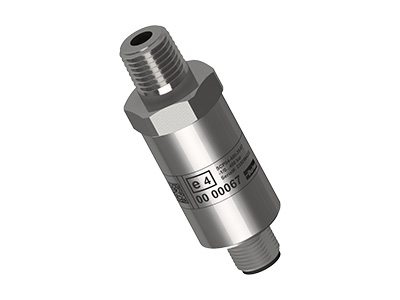
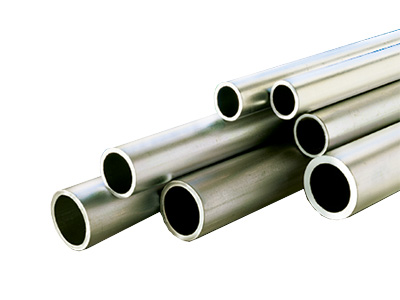
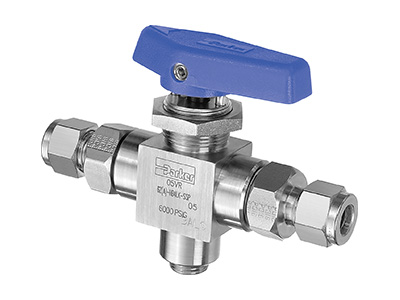
Related products:
- Seal-Lok™ Xtreme Tube Fittings
- O-Lok® / Seal-Lok™ H22/H2P Tube Fittings
- Two Ferrule Tube Fittings A-LOK®
- Single Ferrule Tube Fittings CPI™
- Pressure Sensor SCP04
- Parker Grade Tube for A-LOK®, CPI™, MPI™, Autoclave, O-Lok® and Seal-Lok™ Tube Fittings
- Ball Valves, Trunnion Style, HB Series
- Ball Valves B Series
- Medium Pressure Fittings Parker Autoclave
SEALING TECHNOLOGY FOR HYDROGEN FUEL CELLS
The use of sealing technology for hydrogen fuel cells
The fuel cell is a compact and powerful energy converter that converts chemical energy directly into electric (propulsion) energy by means of cold combustion, for instance on board of vehicles. Sealing of the individual components of the fuel cell stack and the supply and discharge lines of the fuel cell requires reliable sealing systems.
Explore the hydrogen fuel cell components
Featured sealing solutions
Sealing solutions from Parker Prädifa are found between the bipolar plates of fuel cells, in threaded connections of pipelines, valves, compressors, and nearly all other required components. These seals excel in terms of their wide temperature range, permeation resistance, mechanical robustness, and scalability to large volumes in mass production. Thermal interface material from Parker Lord and Parker Chomerics complement the offering.
Learn more about sealing solutions for hydrogen consumption:
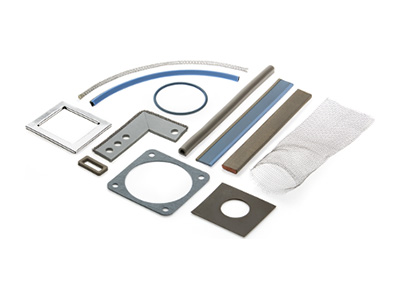
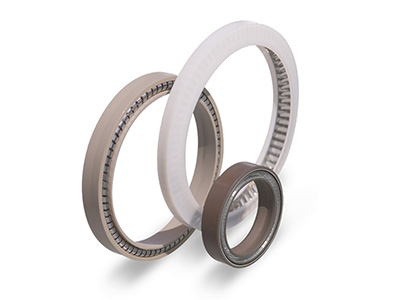
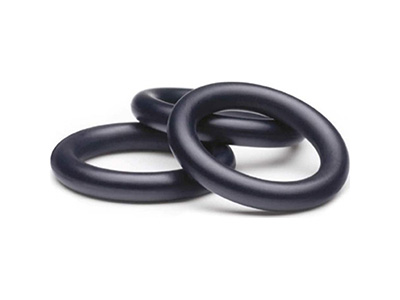
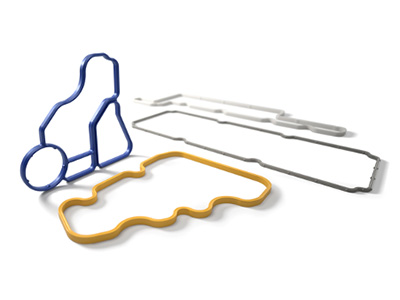
Related products:
- Seals for Bipolar Plates
- CliPHvent Pressure Relief Valve
- Dynamic Seals (e.g. C1 Rod Seal)
- Press-in-Place Seals
- Warp Seals
- EPDM O-Ring (E8556)
- Chlorine-Butyl O-Ring (B8885)
- O-Rings FKM (V8771)
- Polyurethane O-Rings V1 (P5009)
- Metal E-Seals
- Metal C-Seals
- PTFE Slipper Seals
- FlexiSeals®
- Composite Sealing Washers
- Thermal Interface Materials
- EMI Shielding Gaskets
- Butyl O-Rings (B0612-70)
- Molded Shapes
- Daimond Seals
- Silicone Cure-in-Place Gaskets (SD101 & SD104)
HYDROGEN INTERNAL COMBUSTION ENGINE
The world is currently pursuing all possible means to reduce global warming emissions from carbon-producing fuels. Hydrogen plays a critical role in creating alternative systems that provide the carbon-free energy required for a sustainable future.
The Hydrogen Internal Combustion Engine (ICE) is one of the pillars towards climate neutrality. It uses the backbone of the internal combustion engine with some modifications that are required for the hydrogen adaptation. Since it doesn’t produce any CO2 emissions and the NOx emissions can be eliminated using aftertreatment systems, the Hydrogen Internal Combustion Electric Vehicle (HICEV) is one of the leading technology solutions to support climate neutrality.
Hydrogen Internal Combustion Engine (ICE) technology
This new technology has several advantages and disadvantages and brings new filtration challenges. Parker is developing several products to support this technology shift. There are new products required such as the hydrogen filter and there are products that need to be upgraded and modified to cope with the challenges that come from burning Hydrogen such as the CCV and oil filtration.
Solutions for hydrogen ICEs
- Crankcase ventilation filtration for hydrogen combustion engines
- Hydrogen filter for hydrogen combustion engines
- High pressure hydrogen valves for hydrogen internal combustion engines
- High pressure hydrogen regulators for hydrogen internal combustion engines
- Low pressure hydrogen valves for hydrogen internal combustion engines
- Hydrogen flow and pressure control modules for hydrogen internal combustion engines
- Fluid conveyance for hydrogen internal combustion engines
- Sealing technology for hydrogen internal combustion engines
- Conveyance solutions for hydrogen internal combustion engine thermal management
CRANKCASE VENTILATION FILTRATION FOR HYDROGEN COMBUSTION ENGINES
For a hydrogen combustion engine to be considered a “zero emission vehicle” the exhaust emissions need to be very low. A high efficiency crankcase ventilation filter is required to remove the oil mist from the blow-by.
In a hydrogen combustion engine, hydrogen can be blown past the piston ring. To maintain the hydrogen concentration in the crankcase below critical limits, additional air can be added, increasing the blow by volume significantly.
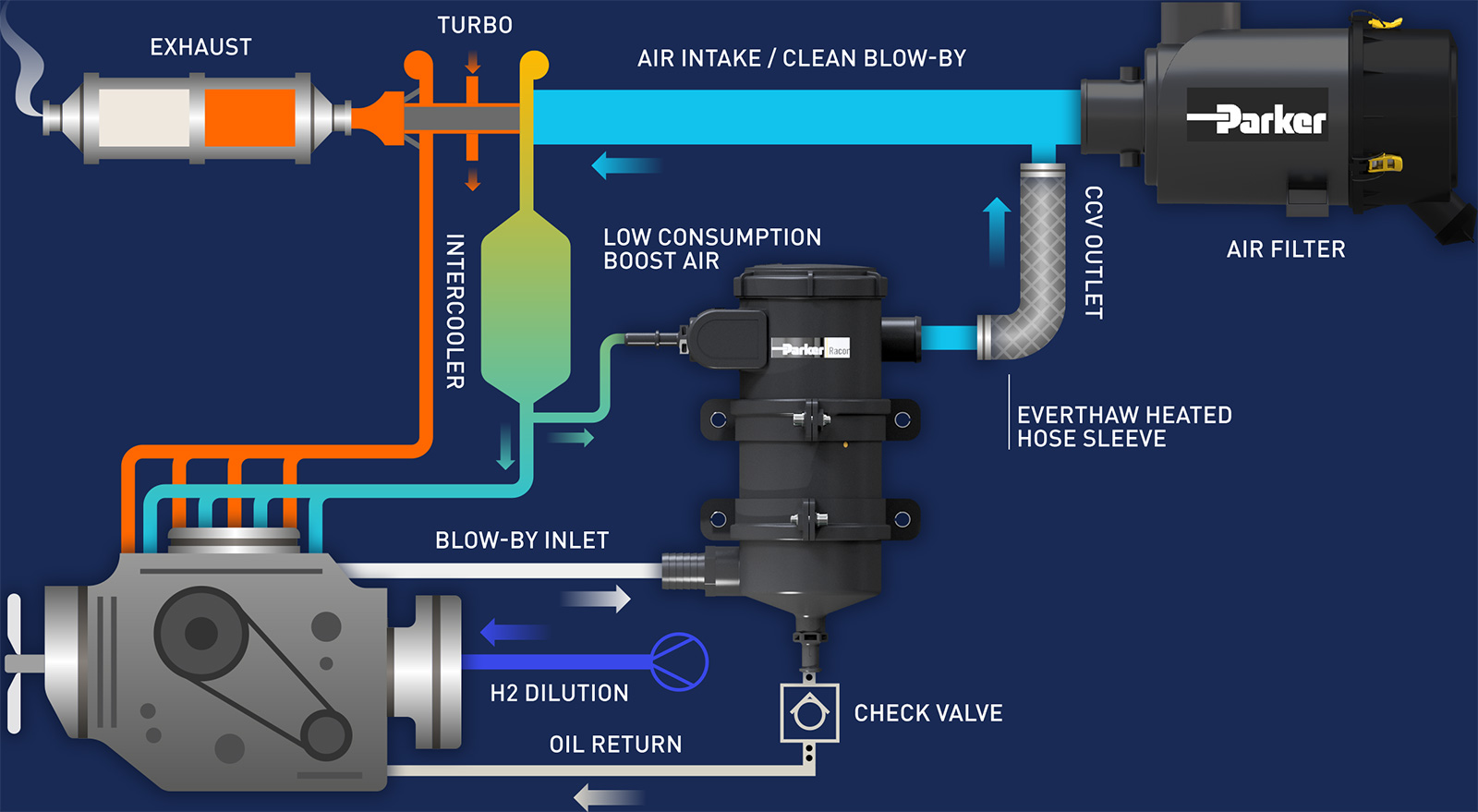
The Super Impactor crankcase ventilation (CCV) filter is the optimal solution to reach strict emission standards. It is an active CCV filter that can be utilized in an open or closed loop. The Super Impactor CCV utilizes a small amount of boost air coming from the turbo that enables it to reach ultra-high efficiencies while showcasing a very good regulation of the crankcase pressure. With a wide range of products, the optimal filter can be selected that can cope with the higher blow-by volume and can reach the ultra-high efficiencies required.
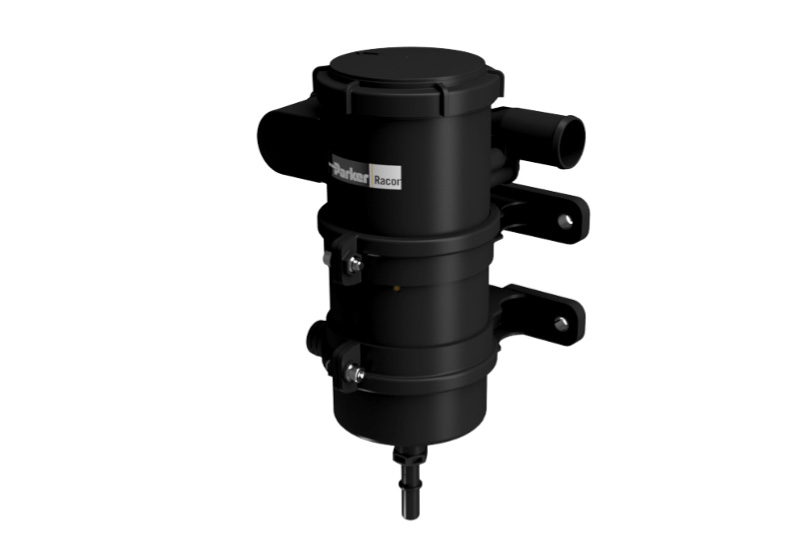
Features and benefits:
• Modular design for a wide flow range
• Up to 99% efficiency (based on engine conditions)
• No moving parts for high durability
• Single or dual stage impactor
• Impactor with second stage media for high efficiency
Specifications:
• Flow Rate from 100 to 1400LPM
• Gravimetric Efficiency up to >99%
• Operating Temperature: -30°C to +130°C
• Crankcase Regulation Pressure: +/- 17mBar
• Continuous Drain
HYDROGEN FILTER FOR HYDROGEN COMBUSTION ENGINES
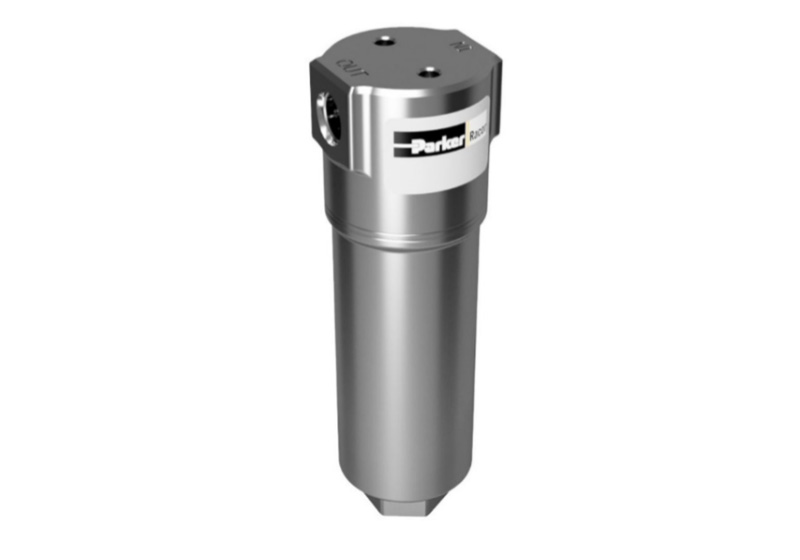
In a hydrogen combustion engine, hydrogen is burned in the engine instead of diesel and this brings several challenges with it. To protect the injection systems from particulates or potentially liquids that can come through the refueling process a hydrogen filter should be installed.
Parker’s Hydrogen Filter will remove particles and coalesce liquids from the hydrogen stream to protect the injection system and the engine.
Features and benefits:
• High efficiency water separation
• Design optimized for automotive market
• Coalescing and particle retention filtration
• Wide range of filtration types
Specifications:
• Filtration efficiency: 99.99% @ 0.3 microns
• Working Pressure: Rated to 55 bar
• Material: Stainless Steel
HIGH PRESSURE HYDROGEN VALVES
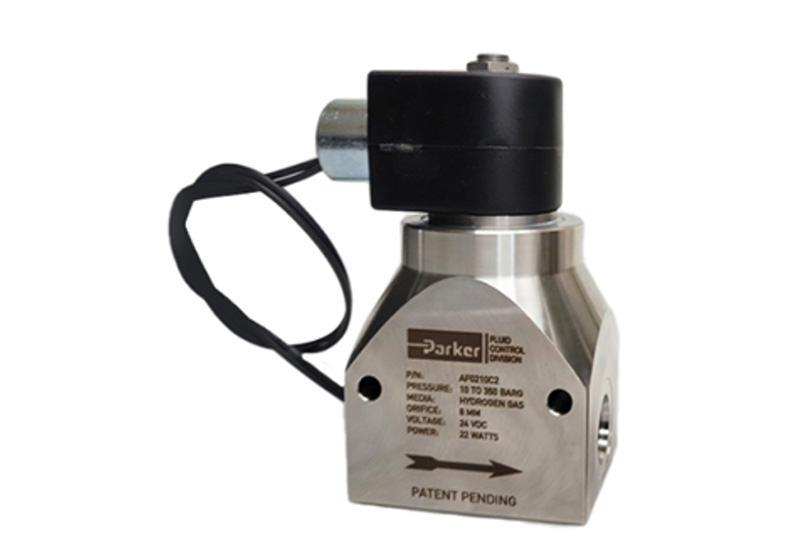
Designed for use in high pressure H2 systems up to 700 bar (10,000 psi), Parker’s hydrogen control valves allow the storage and use of hydrogen in fuel cell powered vehicles resulting in zero emissions.
Parker’s High Pressure Shut-Off Valve helps protect the fuel cell system from high tank pressures.
Features and benefits:
• Indirect pilot operated normally closed valve with precision orifice
• Stainless steel liner for additional stability against strain
• Wear compensating spring design
• Conduit sealing for protection in harsh environments
• High magnetic efficiency
• Redundant external seals
Specifications:
• Cv ~ 2.5
• Standard 22 watt fused Haz Loc coil
• 450G Peek construction for high pressure longevity
• Numerous connection options
HIGH PRESSURE HYDROGEN REGULATORS
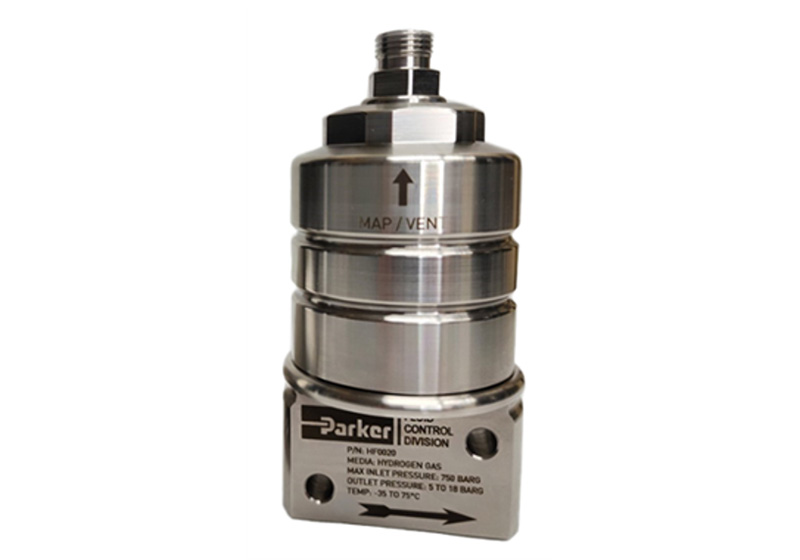
Designed for use in high pressure H2 systems up to 700 bar (10,000 psi), Parker’s hydrogen regulators allow the storage and use of hydrogen in fuel cell powered vehicles resulting in zero emissions.
Parker’s pressure reducing regulator controls H2 pressure levels for safe and efficient flow to the fuel cell stack.
Features and benefits:
• Heavy duty 316L stainless steel construction for harsh transportation applications
• Friction damped piston and poppet to reduce flow oscillation
• Pressure balanced poppet for reduced supply pressure effect
• Sealed bonnet and vent fitting for controlled external leakage
• Dome pressure bias capable (1:1) ratio for turbocharged ICE applications
• Low internal leakage (creep) design
• Wear resistant internals
Specifications:
• H2 compatible materials of construction
• Various outlet pressure levels available with tolerance ±1.0 bar at mass flowrate of 6 g/sec H2
• SAE J1926 o-ring and threaded cone & sleeve porting
• Multiple mounting options
LOW PRESSURE HYDROGEN VALVES
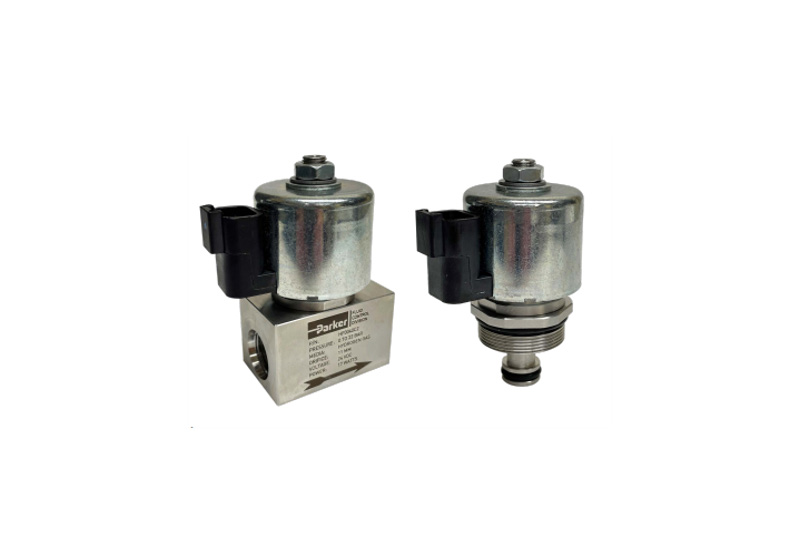
Designed for use in H2 systems, Parker’s hydrogen control valves allow the storage and use of hydrogen in fuel cell powered vehicles resulting in zero emissions.
Parker’s Low Pressure Shut-Off Valve helps allow proper control of hydrogen to the fuel cell stack.
Features and benefits:
• H2 material compatibility
• Optimized design to enable high flow coefficient in a compact size
• Different coils and connections available
• Cartridge version available for design flexibility
Specifications:
Valve function: 2/2 normally closed
• Maximum operating pressure: 22 barg
• Operating temperature: -40°C to +85°C
• Valve Body: 316L SS, Ports SAE J1926(-8, ¾-16 UNF)
• Orifice diameter: 0.43 in (11mm)
• Coil: 12VDC or 24VDC/17W, DT04-2P Deutsch connector, UL Class H(180C) Coil Encapsulation, IP69K moisture protection
• Internal seal material: HNBR / Buna-N
• Internal component materials: austenitic and ferritic stainless
H2 FLOW AND PRESSURE CONTROL MODULES
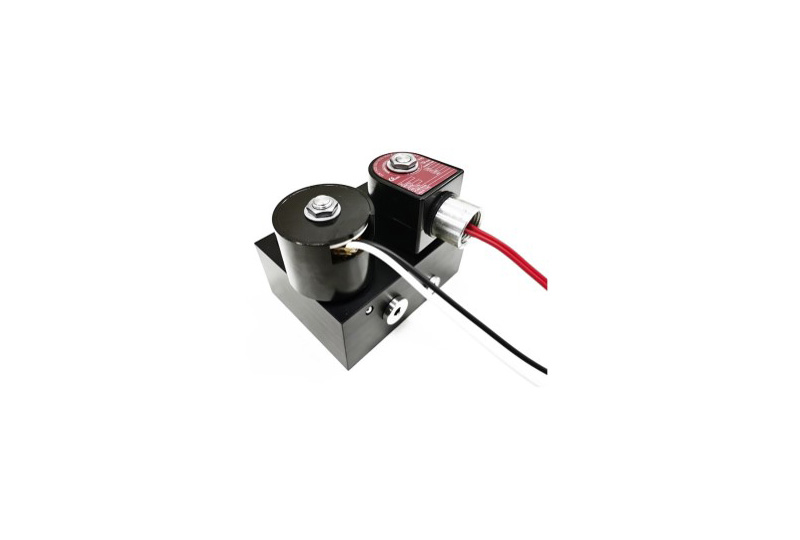
Designed for use in H2 systems, Parker’s hydrogen control modules allow the storage and use of hydrogen in fuel cell powered vehicles resulting in zero emissions.
Parker’s H2 flow & pressure module allows precise control of H2 to the fuel cell stack.
Features and benefits:
Integrated module with on-off, proportional, and exhaust control capabilities
• Less than 0.25 cc/min leakage at 20 barg
Specifications:
Aluminum body, HBNR seals, stainless steel components
• BSP standard connection with other options available
• Fluid temperature -40°C to 120 °C
• On-Off operating pressure 0-20 barg, orifice 8mm, working voltage 18-32VDC
• Proportional operating pressure 8-12 barg, orifice 3mm, flow 600L/min @12bar input, working voltage 20.5-32VDC
• Exhaust cracking pressure 1.9-2.1 barg, orifice 5mm
FLUID CONVEYANCE FOR HYDROGEN INTERNAL COMBUSTION ENGINES
The use of fuel conveyance technology in Hydrogen Internal Combustion Engines (ICE)
Our hydrogen-compatible fluid conveyance products for Internal Combustion Engines (ICE) enable safe and efficient operation. One of the main challenges in using hydrogen as a fuel source is the risk of leakage or combustion, which can lead to safety hazards. Therefore, fuel conveyance products for ICEs must be designed to prevent leaks and ensure that the fuel is delivered to the engine in a controlled and safe manner.
Featured fitting, sensor, valve and regulator products
Parker solutions, from small bore fittings and tube to solenoid valves for gaseous and liquid Hydrogen come in a range of sizes, pressures, and temperatures are critical on-board hydrogen vehicles that utilize internal combustion engines. Fuel conveyance products from Parker are used in the fuel delivery system that enable the safe and efficient transfer of hydrogen fuel from the storage tank to the engine.
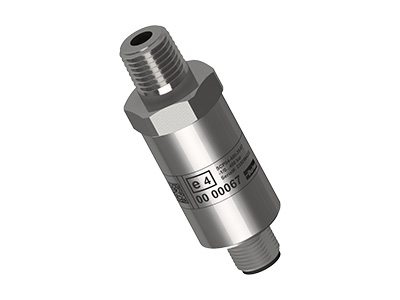

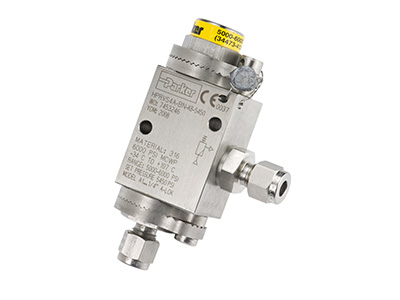
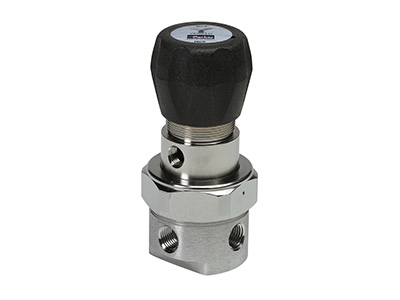
Related products:
- Pressure Sensor SCP04
- Two Ferrule Tube Fittings A-LOK®
- Single Ferrule Tube Fittings CPI™
- Proportional Relief Valves HPRV Series
- Pressure Regulators IR4000 Series
- H2 Fuel Regulation Module
- H2 Pressure Regulator
- 2/2-way and 3/2-way Solenoid Valves
- H2 Rail Pressure Control Solenoid Valve
- H2 3/2-way Diverting Solenoid Valve
- 2/2-way High Pressure Solenoid Valve
SEALING TECHNOLOGY FOR HYDROGEN INTERNAL COMBUSTION ENGINES
The use of sealing technology for hydrogen-powered vehicles
Hydrogen is suitable as an alternative energy source for road-going vehicles. Here it can be burned directly in an internal combustion engine. The basic design of hydrogen-powered vehicles is very similar to that of vehicles with gasoline engines. Even so, there are some components with differentiating characteristics such as high-pressure tanks and valves, pressure reducers and low-pressure lines.
Featured sealing solutions
For hydrogen combustion engines, solutions that have been proven in use for decades are available. Seals used in these applications are elastomeric O-rings as well as molded parts made of specialty butyl, EPDM, polyurethane, or FKM materials, depending on temperature and pressure requirements. Where elastomers cannot be used, PTFE or metal seals are selected.
Learn more about sealing solutions for hydrogen consumption:
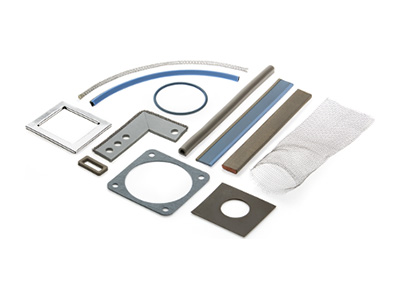
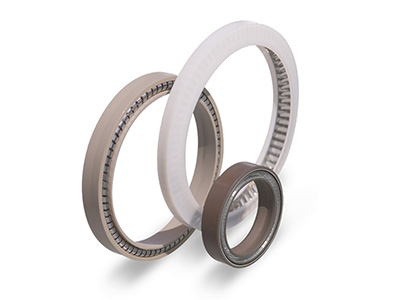
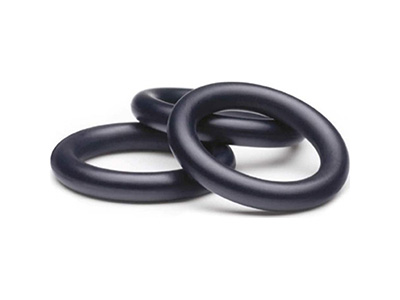
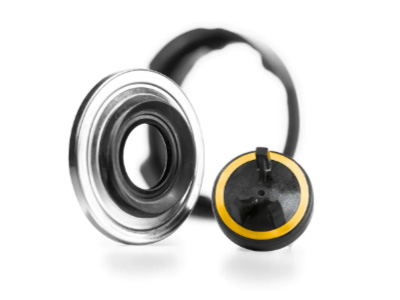
Related products:
CONVEYANCE SOLUTIONS FOR THERMAL MANAGEMENT
Liquid cooling solutions for vehicle systems
Effective heat transfer and dissipation is paramount for optimized vehicle efficiency, range, and component/battery longevity. Whether designing vehicle prototypes or high production systems, Parker’s components play a key role in providing an optimized vehicle thermal management system.
Featured liquid cooling conveyance products
Parker’s transportation liquid cooling products are specifically designed to meet the key pressure, temperature, weight, and serviceability requirements of liquid cooling circuits for vehicle battery and electrification systems. Liquid-cooled batteries, inverters, e-motors, and other subsystems require lightweight, flexible, high-flow, and push-to-connect (PTC) product features. Parker’s liquid cooling products meet these requirements and provide reliability, speed, and flexibility to OEM, fleet, and aftermarket channels. Parker’s collaborative approach to developing custom thermal management solutions provides improvements in system cooling, OEM installation efficiency, and end-user service intervals.
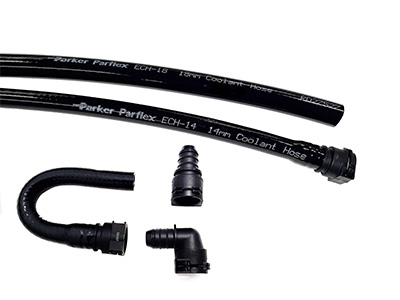
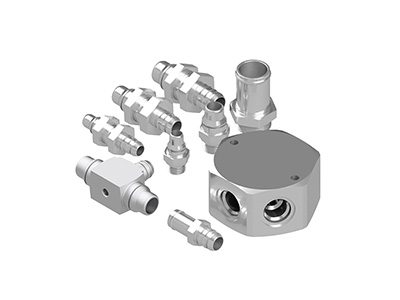
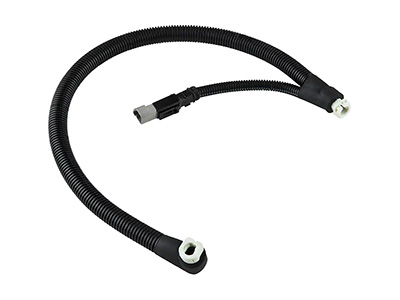
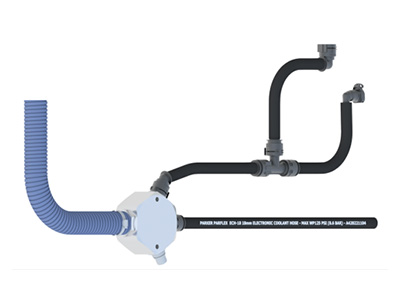