ELECTROLYZER
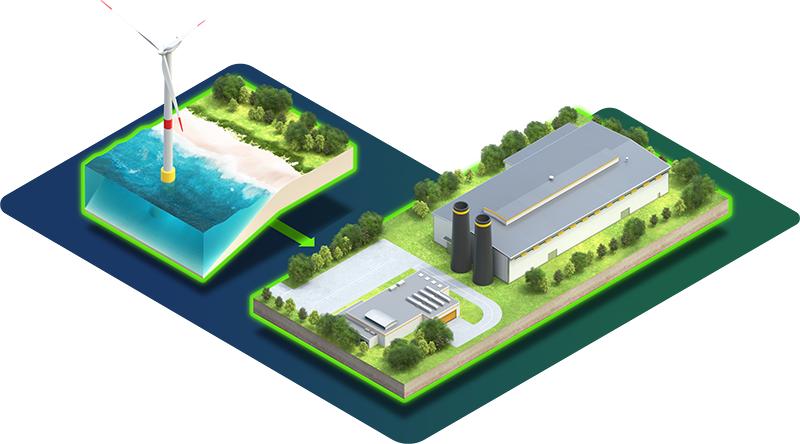
Green Hydrogen
Green hydrogen is made by using clean electricity from surplus renewable energy sources, such as solar or wind power, to electrolyse water. The hydrogen produced can be stored as a gas or liquid and can be used for a wide range of industrial processes, significantly reducing emissions.
Green hydrogen production through electrolysis
In green hydrogen production, electrolysis is used to break down water into its individual elements; hydrogen (H2) which is compressed and sent to storage, and oxygen (O2) which is either also stored or vented to the atmosphere.
There are several different electrolyzers that can be used:
Proton Exchange Membrane (PEM) electrolyzers
PEM electrolyzers use a solid polymer electrolyte that only allows hydrogen ions (protons) to pass through to form hydrogen gas on the cathode side.
Alkaline electrolyzers
Alkaline electrolyzers use an electrolyte solution (usually potassium hydroxide) which allows hydroxide ions through leaving hydrogen gas bubbles.
Solid oxide electrolyzers
A solid ceramic material is used as the electrolyte at high temperature. Water is used in the form of steam which results in higher energy but produces ultra-pure hydrogen with great efficiency.
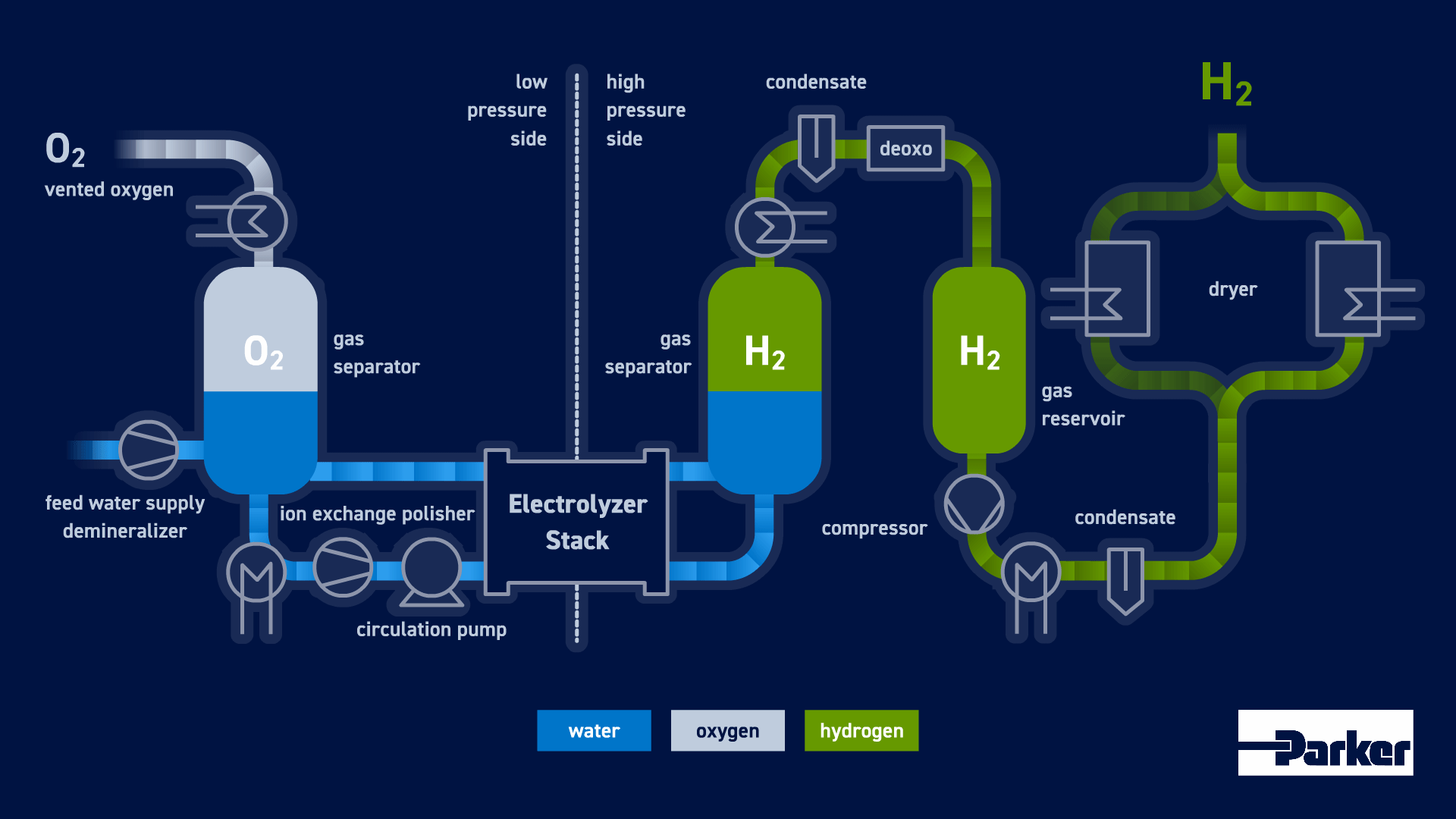
Solutions for green hydrogen production
Regardless of the electrolyzer type, Parker technologies are essential to protect the process, to maintain efficiency and to purify the hydrogen gas stream to the required high standard. Parker’s broad filtration portfolio includes liquid filtration, gas separation, purification, cooling, hydraulics, fluid conveyance and sealing.
ELECTROLYZER FEEDWATER PURIFICATION
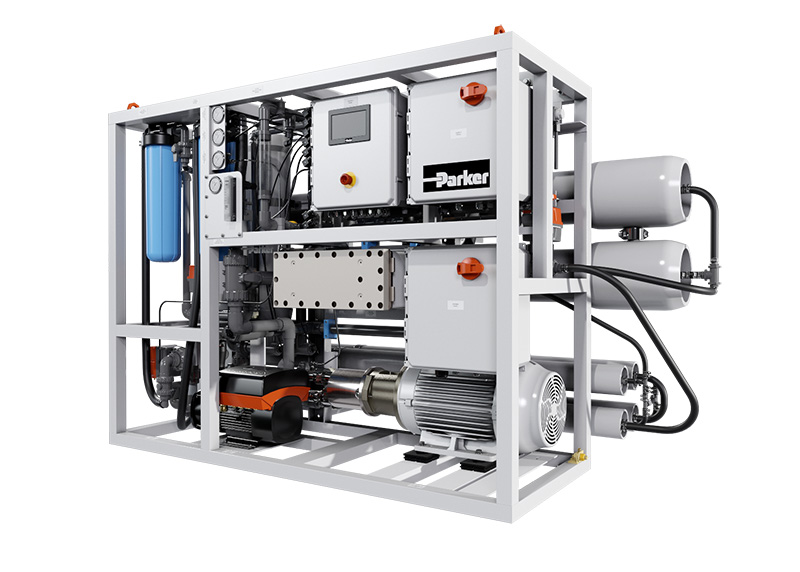
Water is the feedstock for green hydrogen production, and it must be treated to ultrapure quality. The water treatment solution required depends on the choice of electrolyzer technology and water source. Inadequate water treatment can jeopardize the operation and damage the electrolyzer.
Parker’s wide range of water purification solutions provide innovative ways to filter, purify, discharge, recapture, recondition or reuse industrial and process water. Our proven industrial and customized membrane and filtration systems blend superior performance with full compliance to deliver optimum reliability in pretested, packaged skids or turnkey containerized solutions for electrolyzer applications.
Related products:
FEEDWATER AND LYE FILTRATION
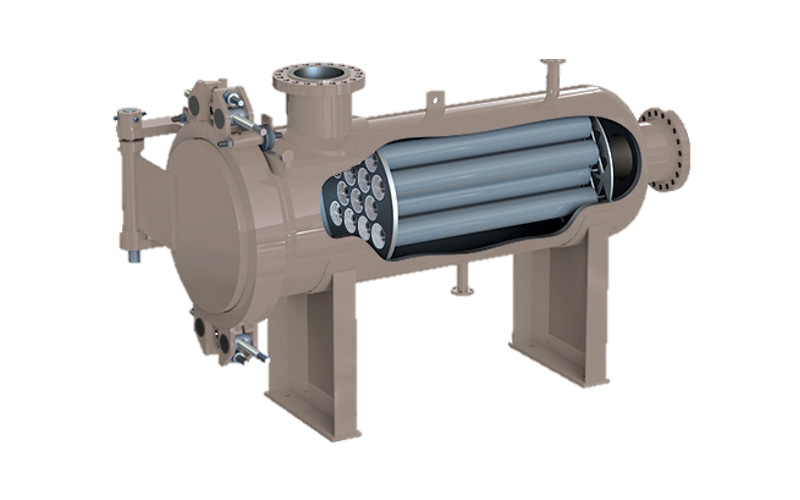
Alkaline electrolyzer technology uses highly corrosive potassium hydroxide 30- 40% (KOH) as the electroyte. In the alkaline electrolser the electrolyte will be separated from the hydrogen and oxygen gas stream and circulated back to the stack again. Due to the corrosive KOH the electrolyzer component will corrode and produce very fine particles. These particles, when not filtered out, will contaminate the stack and other components with the result of lower efficiency and a shorter lifetime of the stack and the electrolyte.
The Parker XtreamPure filter offers high performance and a smaller vessel footprint which are important to maintaining a clean electrolyte stream. The vessel is designed with large diameter cartridges that allow for high flow rates which significantly reduces the number of cartridges to change out. With a wide variety of cartridge options, the XtreamPure filter is sure to be a winner for filtering your electrolyte stream!
Related product:
ELECTROLYZER GAS / WATER SEPARATION (HYDROGEN AND OXYGEN)
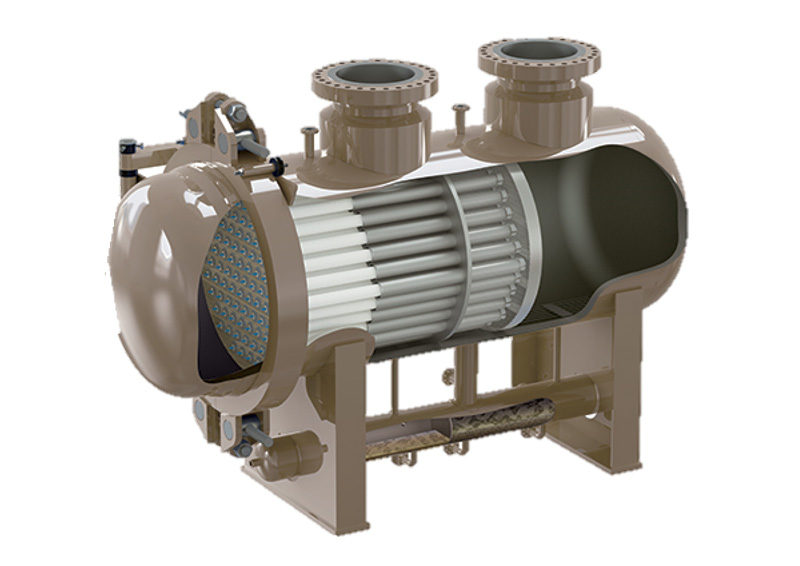
When it comes to removing bulk water from gas streams on an electrolyzer (both hydrogen and oxygen) a plant operator will generally want to remove as much water as possible with an efficient and compact solution. Removing water or electrolyte from the hydrogen stream coming off the electrolyzer stack is one such area where effective removal of water / electrolyte can reduce product loss, downstream corrosion, contamination, and damage to equipment such as compressors, molecular sieve dryers, and blowers. The other benefit about high efficient water removal is that the demineralized water production system can produce less water.
For electrolyzer applications, Parker has developed a unique Gemini solution which combines bulk water separation, high efficiency gas coalescing (utilising Parker’s proprietary PEACH technology) and degassing - prior to the separated water being returned to the stack. By combining multiple filtration and separation technologies into one system, customers can benefit from increased efficiency, and reduced complexity, cost and footprint. The Gemini solution can be used to separate bulk water from both hydrogen and oxygen gas streams.
Related product:
ELECTROLYZER SYSTEM PURGE

Upon start up and following electrolyzer system maintenance, a nitrogen purge may be required. Nitrogen gas can be supplied in a variety of methods, including gas cylinders or liquid nitrogen dewars. Depending on the electrolyzer location, there may be challenges with traditional gas supply methods, such as logistical issues, safety concerns and high costs (delivery, rental of cylinders, cost of gas).
Parker offers a wide range of Nitrogen Generators – based on two technologies – pressure swing adsorption and proprietary hollow fibre membrane. The systems enable customers to generate their own gas - on site, safely and conveniently. Compressed air delivered to the generator is separated and the nitrogen can be delivered at the purity required for the customer application. The systems are incredibly reliable, require minimal maintenance and offer >10 years’ service life.
Related product:
ELECTROLYZER COOLING
The two most established processes for green hydrogen production are alkaline water electrolysis and proton exchange membrane (PEM) electrolysis. In both processes, a liquid is recirculated over an electrolyzer stack to form hydrogen and oxygen. During the electrolysis process, heat is released, which needs to be cooled away to prevent the electrolyte solution from boiling and evaporating, which can be dangerous and reduce the efficiency of the reaction. Further downstream, the hydrogen is compressed, which requires compression interstage and aftercoolers. A closed loop of water or water-glycol mixture is used to cool all the different coolers in the hydrogen production process. And the closed loop is cooled in a central system.
Parker can offer the following solutions for electrolyzer cooling: -
Hyperchill process gas chillers
Extremely compact and easy to use, Hyperchill and Hyperchill Plus-E Chillers are designed for safe and reliable operation in various working conditions while providing a precise and accurate control of the process fluid temperature. The availability of a wide range of accessories and options makes Hyperchill and Hyperchill Plus-E a very flexible solution that fits the needs of all industrial applications.
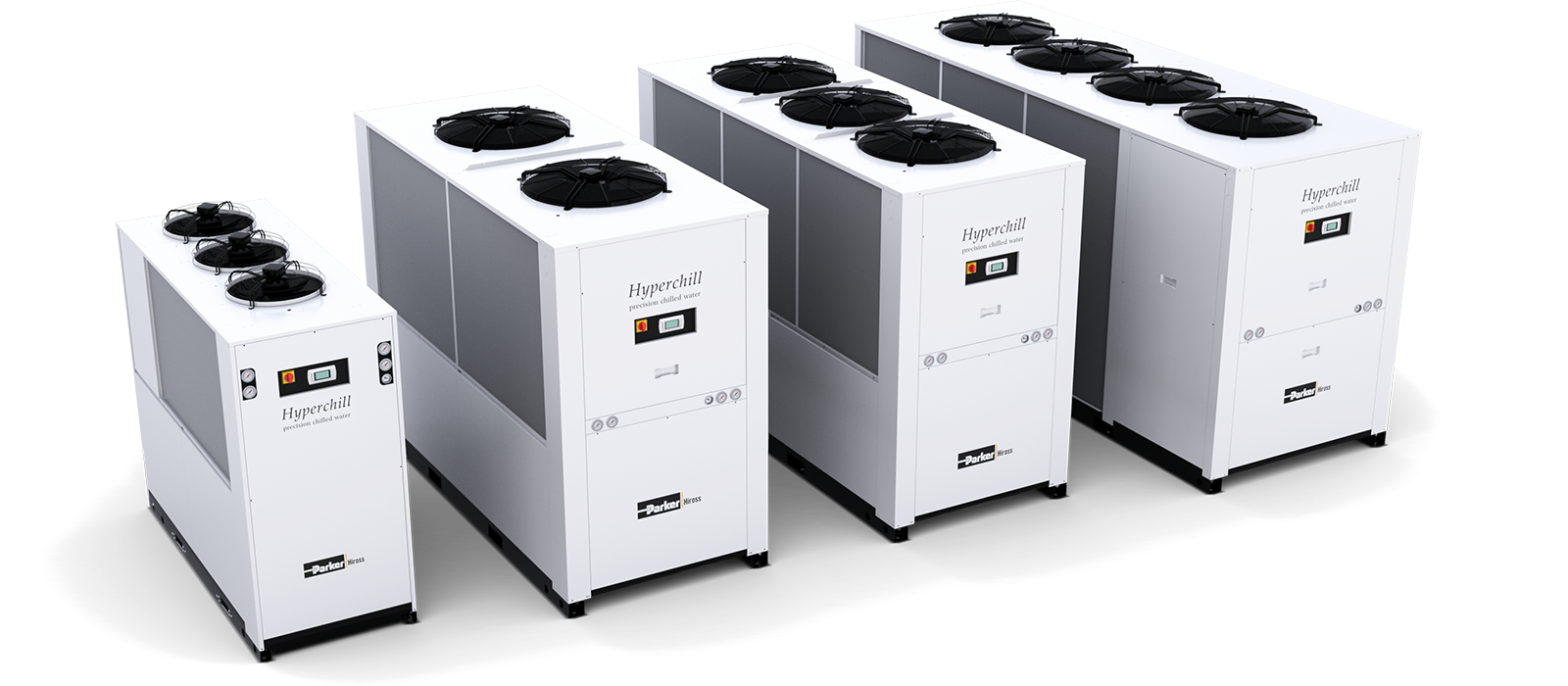
Reference Materials:
Heatric printed circuit heat exchanger

Parker’s Heatric Printed Circuit Heat Exchangers (PCHEs) are a compact, high-performance and bespoke solution optimized for hydrogen processing and conditioning. Up to 85% smaller and lighter than traditional heat transfer technologies, with multi-steam capability, the Heatric PCHE minimizes footprint and pipework complexity through compact engineering and design.
Heatric PCHEs are manufactured sing a specialized solid-state joining process known as diffusion-bonding. This process creates a heat exchanger core with no joints, welds of points of failure. The resulting unit combines exceptional strength and integrity with high efficiency and thermal performance to enable modern energy applications.
Reference Materials:
Liquid coolers with AC motor

The Parker Liquid Cooler with AC Motor (LAC) and Quiet Liquid Cooler with AC Motor (QAC) removes excess heat from the electrolyzer by circulating a coolant through a heat exchanger, which is in contact with the electrolyte solution. The coolant absorbs the excess heat and carries it away from the electrolyzer, thereby maintaining a safe and stable operating temperature. The Quiet Liquid Cooler with AC Motor (QAC) is optimized for low sound level.
Related products:
HYDROGEN GAS PURIFICATION

Parker offers a wide range of purification solutions including filtration and adsorption technologies which are scalable in terms of gas flow rate and pressure. For hydrogen gas, we develop customized solutions, utilising temperature swing adsorption (TSA) drying and de-oxo technologies - designed to consider any space limitations within the electrolyzer. On-line gas monitoring is also available as an option.
Contact us about your electrolyzer applicationELECTROLYZER HYDRAULIC POWER

Hydraulic power units play a critical role in hydrogen production, providing the necessary force and pressure to drive the electrochemical reactions that generate hydrogen from water.
Hydraulic pumps and high-pressure bladder accumulators are also commonly used in electrolyzers to store and regulate the pressure of the hydrogen produced, ensuring the safe and efficient production of hydrogen. Additionally, by storing the hydrogen at high pressure, it can be more easily transported and used as a fuel source for a variety of applications, including transportation and energy production.
Hydraulic power unit for PEM electrolyzers
For a 24 MW PEM electrolysis demonstration plant to supply green hydrogen for ammonia production, Parker supplied a tailored hydraulic power unit designed for an operating pressure of up to 400 bar. To increase efficiency, the unit is built as a stack. It operates three large cylinders that compress the stack and eight small cylinders that act on the proton exchange membrane.
High pressure bladder accumulators
Parker’s EHV High Pressure Bladder Accumulator is specifically designed for hydrogen applications. As the hydrogen gas is produced in the electrolyzer, it is fed into the gas chamber of the accumulator, causing the bladder to compress and the hydraulic fluid to be displaced into a separate hydraulic chamber. This allows the pressure of the hydrogen gas to be regulated and maintained at a constant level, preventing over-pressurization of the system, which could result in equipment failure or even explosion.
Hydraulic pumps
Parker offers multiple hydraulic pump technologies which will create an optimized and customizable system, ensuring pressure and flow performance at the highest levels of system efficiency. Parker’s PVplus piston pump is optimized for heavy duty applications and used to pressurize the hydraulic fluid and maintain a continuous flow within the system. Vane pumps offer high volumetric efficiency to displace a large volume of hydraulic fluid. Meanwhile they provide smooth operation which reduces the likehood of pressure fluctuations that could impact the electrolyzer’s performance. The high efficient Parker bent axis design pumps, with unique spherical piston concept, gives thermal shock resistance. The well proven gear synchronization and double tapered bearing concept gives a very robust and reliable pump in demanding applications, applicable for both open and closed loop systems. Combined with our well proven track record of durable pumps, we have an outstanding uptime. Parker’s high efficient variable truck pump, VP1, with wide displacement range, light weight, tandem mount feature and robust design makes it an outstanding choice when building an energy efficient system.
Related product:
FLUID CONVEYANCE FOR GREEN HYDROGEN PRODUCTION
The use of fluid conveyance technology in electrolysis
Fluid conveyance on a green hydrogen electrolyzer refers to the system of fittings, connectors, valves, hose and tube used to transfer fluids, such as water and electrolyte, to and from the electrolyzer cells. Parker’s products are designed to handle the pressures and temperatures required for the electrolysis process and are manufactured in a range of corrosion resistant alloys.
Featured fittings, connectors, regulators, sensors and hose products
Parker’s fluid conveyance solutions for green hydrogen electrolyzer applications are specifically designed to optimize uptime. Small bore connectors, couplings, hose, sensors and tubing are all used to control pressure, temperature, and flow of gas and liquids while ensuring a leak-proof connection. All of these solutions provide the necessary connections and flow control to ensure the safe and efficient operation of the electrolyzer.
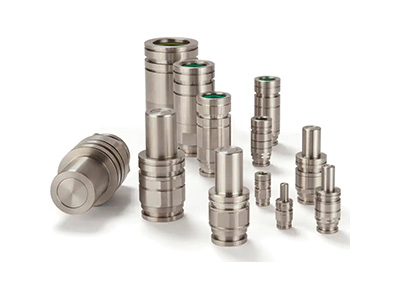
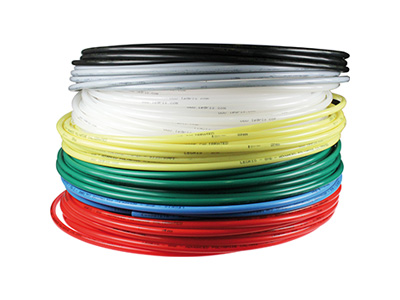
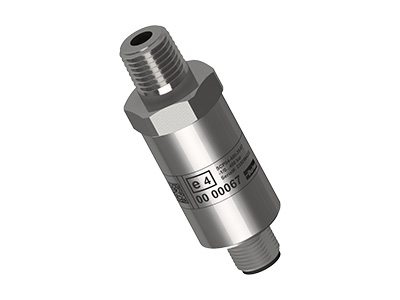
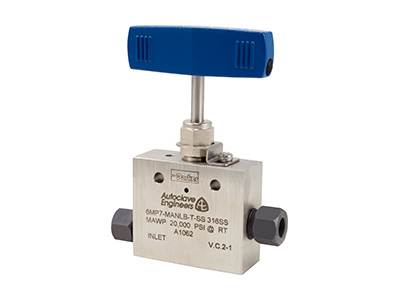
Related products:
- Pressure Sensor SCP04
- 316L Stainless Steel Push-In Fittings LF 3800
- Dry Break Quick Coupling with Parker Profile Series 200
- Quick Coupling Series 20
- Quick Coupling Series 21
- Quick Coupling Series 25
- Quick Coupling Series 27
- Parflange® F37 Non-Welded Piping Systems
- Two Ferrule Tube Fittings A-LOK® Series
- Single Ferrule Tube Fittings CPI™ Series
- Permanent Tube Fittings Phastite® Series
- Nylon Tubing
- Medium Pressure Needle Valves 20SM Series Parker Autoclave
- MPI Needle Valves MAN Series
- Medium Pressure Check Valves Parker Autoclave
- Pressure Regulators IR4000 Series
- Isolation Ball Valves Hi-Pro Series
- Ball Valves B Series
- Ball Valves, Trunnion Style, HB Series
- Compressed Natural Gas Hose
SEALING TECHNOLOGY FOR GREEN HYDROGEN PRODUCTION
Efficient hydrogen production requires large electrolysis systems that are demanding on the sealing systems due to their sheer size. For alkaline electrolyzers chemical resistance and service life are particlularly important while PEM electrolyzers require low-permeation sealing solutions. Solid oxide electrolyzers, due to high operating temperatures, call for non-polymer sealing solutions such as metallic sealing systems.
Featured sealing solutions
High thermal requirements, extreme pressures, and chemical resistance are key challenges to be met by sealing systems in electrolyzers. Parker Prädifa offers suitable seal materials and specialty seal designs – also available in very large dimensions – that withstand such extreme conditions. In addition to meeting these requirements, our sealing solutions, especially those for bipolar plates or other seals close to the stack, have a functionally reliable and easy to install design to enable cost-efficient mass production of electrolysis systems.
Learn more about sealing solutions for hydrogen production:
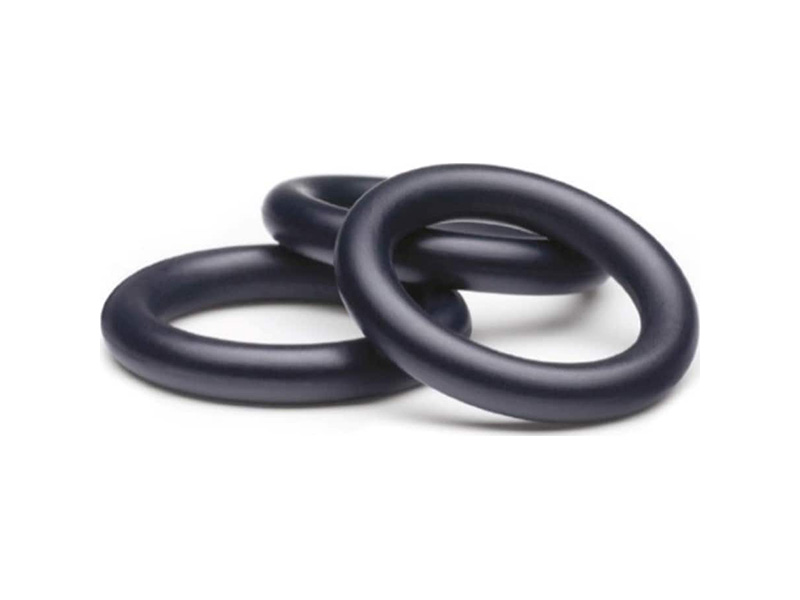
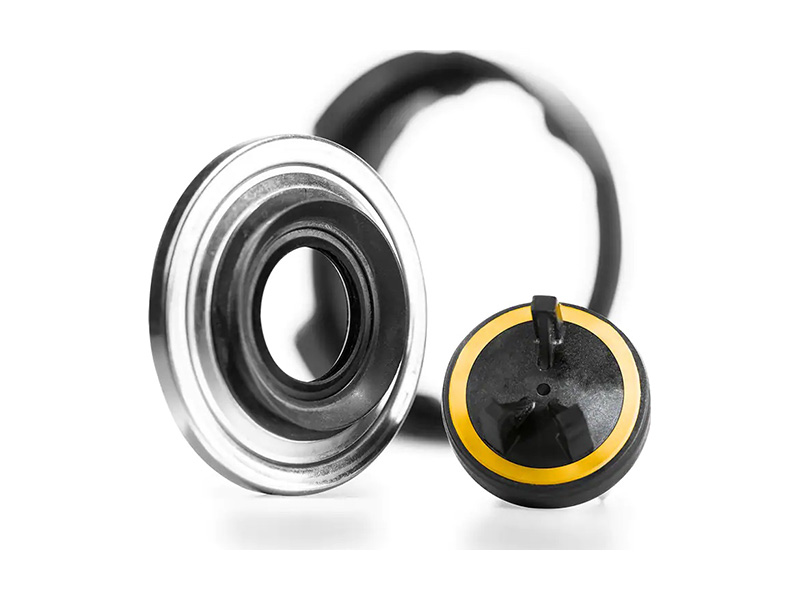
Related products:
STEAM METHANE REFORMING
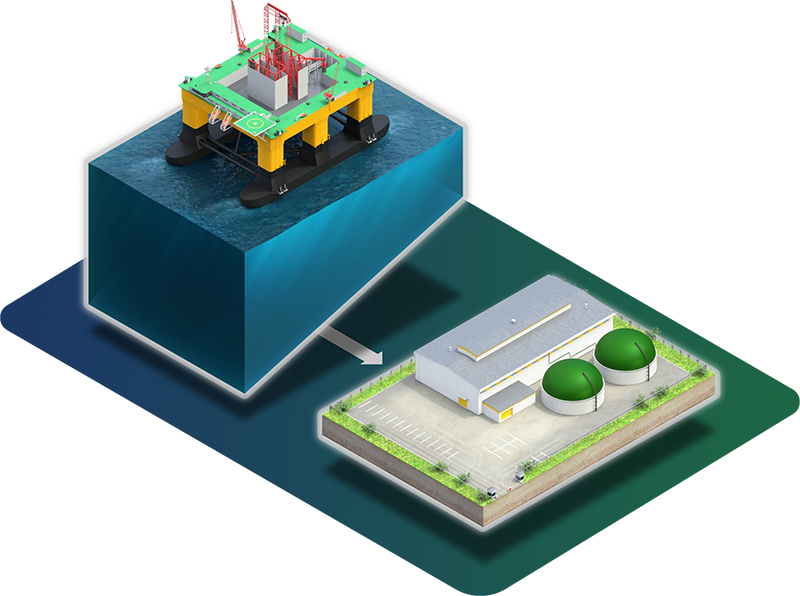
Grey Hydrogen
Grey hydrogen is currently the most common form of hydrogen. It is produced from fossil fuels (methane) via steam methane reformation or autothermal reforming. All grey hydrogen production releases carbon dioxide into the atmosphere.
Hydrogen production through steam methane reforming (SMR)
During the SMR process, methane is heated with steam under pressure in the presence of a nickel or platinum catalyst. This produces hydrogen, carbon monoxide and a relatively small amount of carbon dioxide.
CH4 + H2O (+heat) → CO + H2
A water-gas shift reaction follows where carbon monoxide and steam are reacted using a metal oxide catalyst to produce additional hydrogen and carbon dioxide.
CO + H2O → CO2 + H2 (+heat)
A final step called pressure-swing adsorption is then used to remove carbon dioxide and other impurities from the gas stream leaving essentially pure hydrogen.
Hydrogen production through autothermal reforming (ATR)
ATR is a process in which methane is reacted with oxygen in the presence of steam or carbon dioxide to produce syngas. The syngas produced is composed of hydrogen, carbon monoxide and carbon dioxide. The process is a partial oxidation where almost all of the carbon dioxide ends up in the pressure swing adsorption tail taking overall carbon dioxide recovery to 98%.
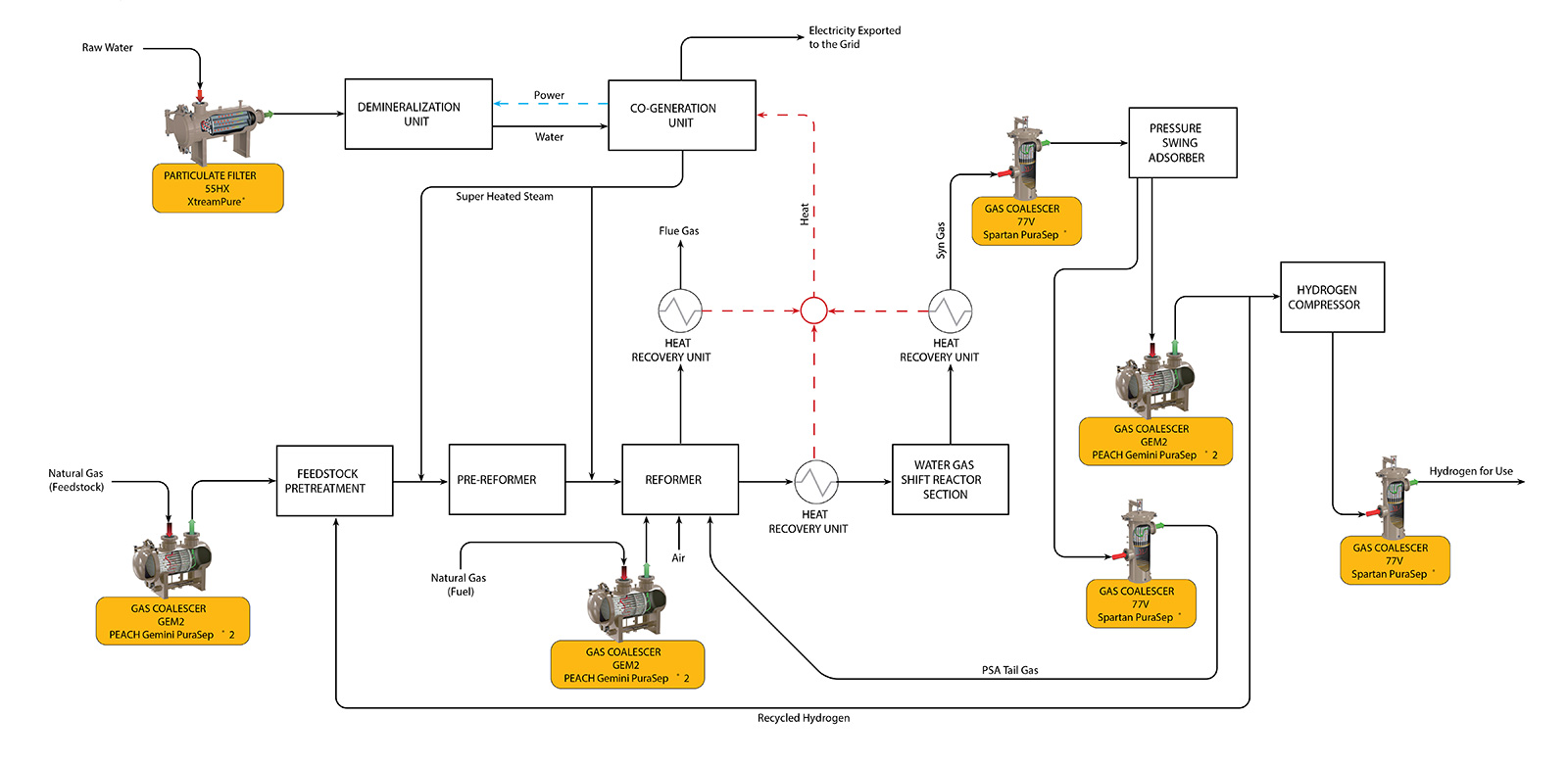
Solutions for grey hydrogen production:
REFORMER FEEDWATER FILTRATION
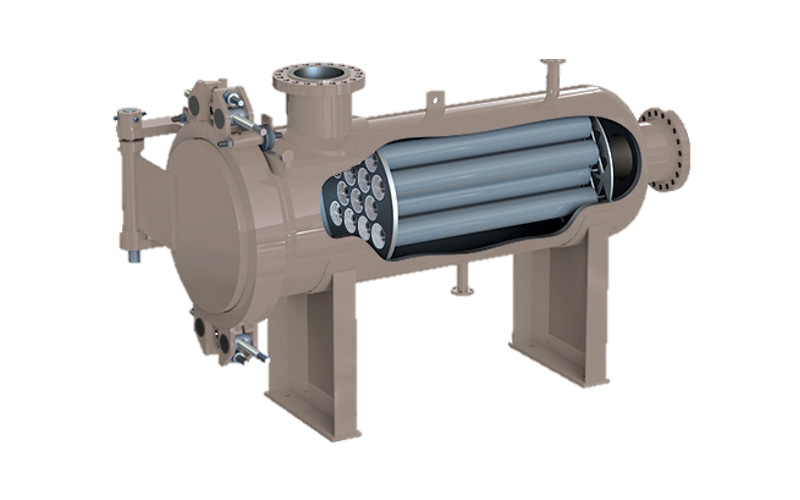
Particulate material carried in the raw water feed can contaminate the demineralisation unit impacting its efficiency and potentially inflicting permanent damage. High performance and a smaller vessel footprint are important to maintaining a clean stream that protects downstream equipment.
Parker’s XtreamPure high flow liquid filter can be used for particulate filtration of reformer feedwater. The system utilizes large diameter filter cartridges, significantly increasing the flow of liquid that can be processed and reducing the number of cartridges to changeout versus traditional filters.
Particulate material carried in the raw water feed can contaminate the demineralisation unit impacting its efficiency and potentially inflicting permanent damage. High performance and a smaller vessel footprint are important to maintaining a clean stream that protects downstream equipment. Parker’s XtreamPure high flow liquid filter can be used for particulate filtration of reformer feedwater. The system utilizes large diameter filter cartridges, significantly increasing the flow of liquid that can be processed and reducing the number of cartridges to changeout versus traditional filters.
Related product:
NATURAL GAS FILTRATION
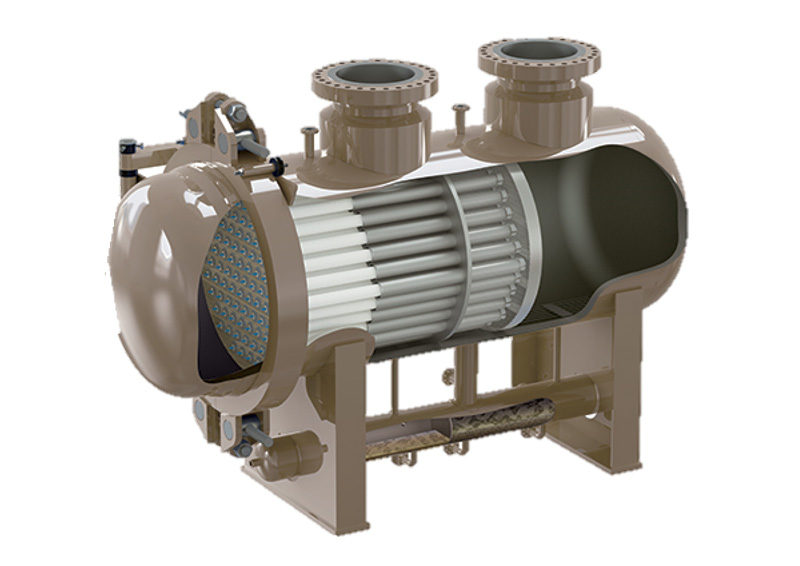
Natural gas feed to the reformer and that used for fuel in the process is loaded with moisture and particulates from piping and other equipment along the transportation network and distribution pipelines. To protect the reformer from damage and ensure optimal performance, particulate and water must be efficiently removed from the gas stream.
The Gemini Gas Coalescer incorporating PEACH coalescing technology has been proven in the oil and gas market for many years - delivering superior performance in a trouble-free design. By combining multiple filtration and separation technologies into one system, customers can benefit from increased efficiency, reduced complexity, cost and reduced footprint.
Related product:
GAS FILTRATION PRIOR TO PRESSURE SWING ADSORBER
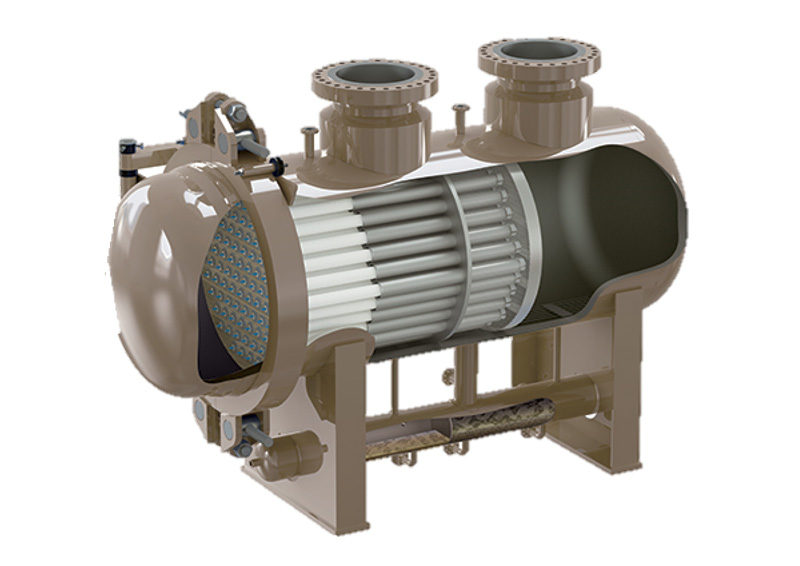
Protecting the PSA from water droplets carryover is key to achieving maximum CO2 adsorption. This is because the higher the pressure, the more gas is adsorbed but when the pressure drops, the gas is released. The stage 1 gas coalescer Spartan will effectively remove water droplets downstream of the PSA and from the PSA tail gas.
The hydrogen gas contains both particulate carryover from the PSA as well as moisture both of which must be removed to protect the compressor. The Gemini Gas Coalescer incorporating PEACH coalescing technology has been proven in the Oil and Gas market for many years - delivering superior performance in a trouble-free design. By combining multiple filtration and separation technologies into one system, customers can benefit from increased efficiency, reduced complexity, cost and reduced footprint.
Related products:
FLUID CONVEYANCE FOR GREY HYDROGEN PRODUCTION
The use of fluid conveyance technology in steam methane reforming (SMR)
Fluid conveyance products such as fittings, piping systems, connectors, and valves are essential components in the steam reforming process.
Featured fittings, connectors, regulators and valve products
Parker’s hydrogen-compatible fluid conveyance products for steam methane reforming enable safe and efficient operation from vacuum to 1034 bar nominal pressure (15,000 psi). Parker solutions, from small bore fittings, couplings, valves, hose, and tube for gaseous and liquid hydrogen in a range of sizes, pressures, and temperatures which are critical, especially in demanding, corrosive, pressured and heat-intensive natural gas environments.

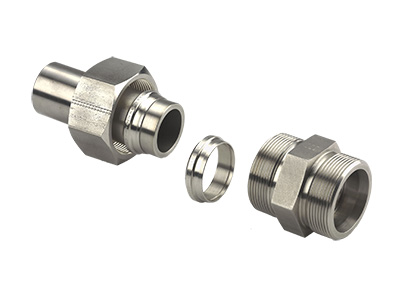
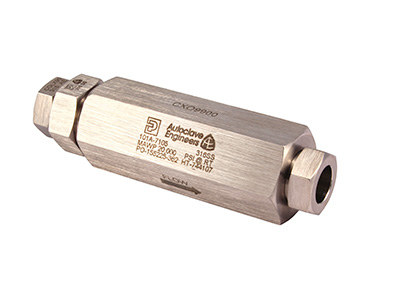
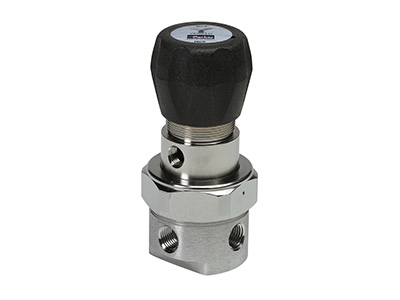
Related products:
- Parflange® F37 Non-Welded Piping Systems
- EO Progressive Ring (DPR) System
- Two Ferrule Tube Fittings A-LOK®
- Single Ferrule Tube Fittings CPI™
- Permanent Tube Fittings Phastite®
- Medium Pressure Needle Valves Parker Autoclave
- MPI Needle Valves MAN Series
- Medium Pressure Check Valves Parker Autoclave
- Isolation Ball Valves Hi-Pro Series
- Ball Valves B Series
- Ball Valves, Trunnion Style, HB Series
- Pressure Regulators IR4000 Series
- Stream Switching Valves
- Modular Sample Conditioning System IntraFlow™
SEALING TECHNOLOGY FOR GREY HYDROGEN PRODUCTION
Sealing solutions are required in many areas of the steam reforming process, both in the reformer itself and in adjacent assemblies such as line connectors, valves, pumps, or storage systems.
Featured sealing solutions
Parker Prädifa offers an extensive range of sealing solutions for a wide variety of steam reforming applications. High-performance FFKM seals are used for sealing hydrogen at up to 240 °C. In other places with lower temperature requirements, more economical EPDM or FKM O-rings can be installed. Using seals made of butyl materials can minimize hydrogen leakage due to particularly high permeation resistance, which may be of crucial importance in storage systems for instance.
Learn more about sealing solutions for hydrogen production:
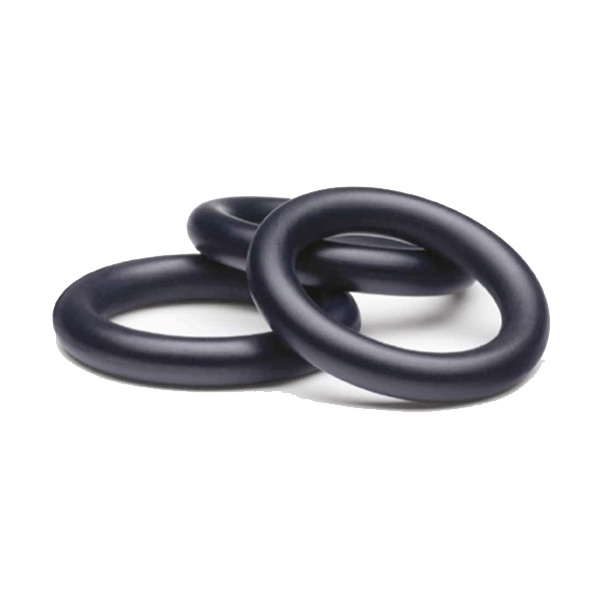
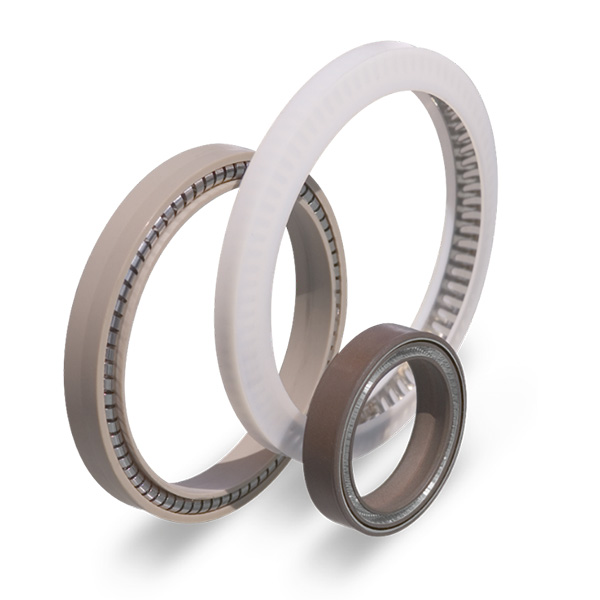

Related products:
CARBON CAPTURE & STORAGE

Blue Hydrogen
Blue hydrogen is produced from natural gas in the same way as grey hydrogen. The key difference is that it is supported by carbon capture and storage (CCS). When CO2 capture is added within the steam methane reforming (SMR) or autothermal reformation (ATR) process, the hydrogen produced can be classified as “blue”.
The carbon dioxide is captured, compressed and stored either permanently or for further use for other applications (termed carbon capture, utilisation and storage or CCUS).
Amine-based carbon capture
One method of CO2 capture or removal is through absorption with solvent based solutions (for example, amines. Amine-based carbon capture is placed before the pressure swing adsorption stage in SMR or ATR as, during this stage, the adsorption material is irreversibly poisoned by hydrogen sulphide.
After the sour gases are absorbed the “rich” amine is then regenerated through a desorber which strips the CO2 before the “lean” amine is looped back to the absorber. The stripped CO2 is compressed before storage.
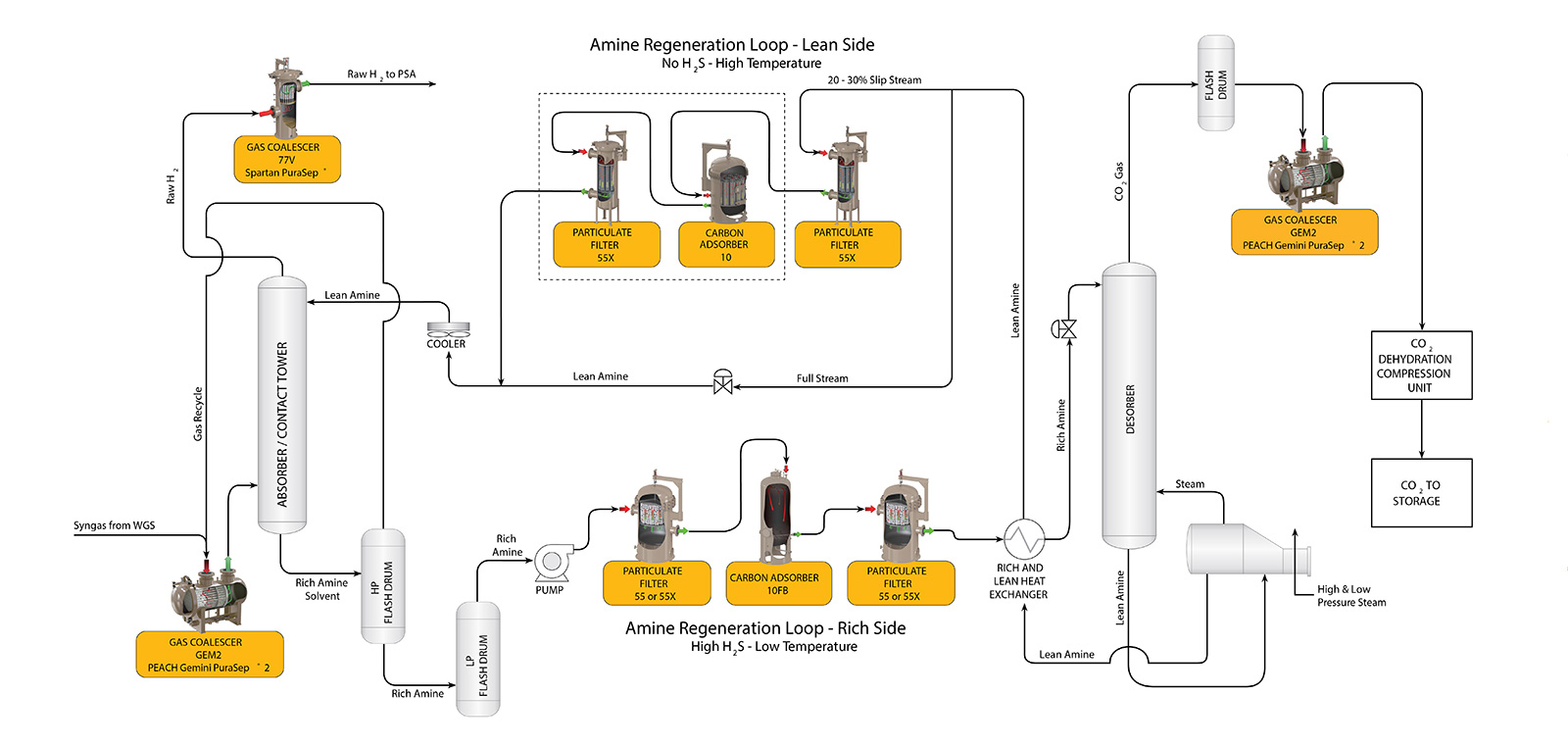
Solutions for blue hydrogen production:
SOUR GAS FEED COALESCING
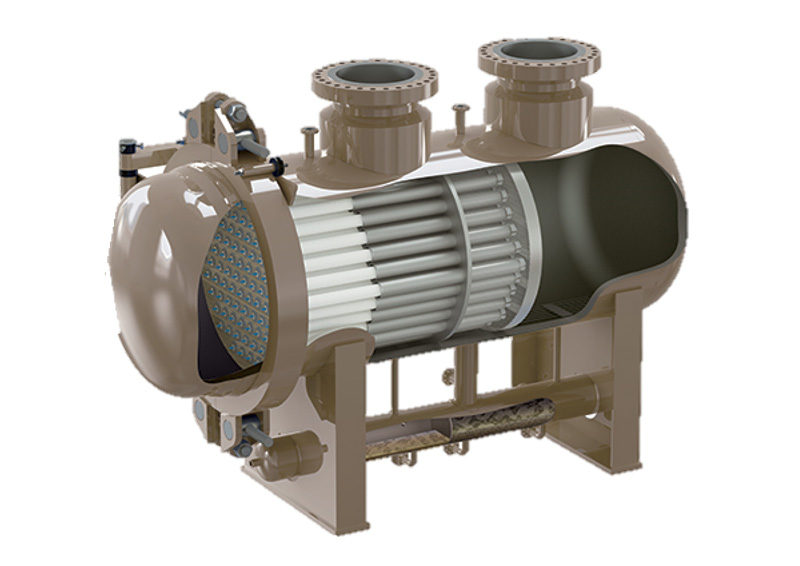
The sour syngas from the water gas shift (WGS) reaction needs to be treated before contacting amine in the absorber tower. Removing particles and water droplets carryover from the WGS reactor is key to keep the highest amine selectivity and avoid foaming.
The Gemini Gas Coalescer incorporating PEACH coalescing technology delivers superior performance in a trouble-free design. By combining multiple filtration and separation technologies into one system, customers can benefit from increased efficiency, reduced complexity, cost and reduced footprint.
Related product:
AMINE LOOP FILTRATION
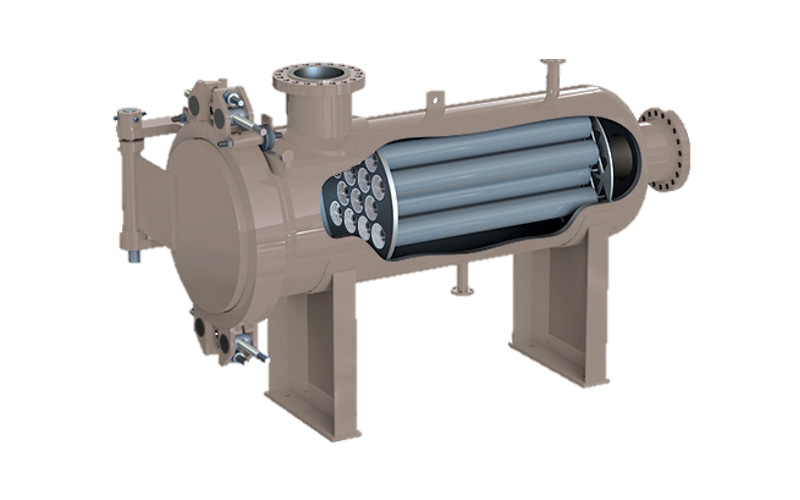
The desorber and its associated heat exchanger and reboiler must be protected to maintain a good temperature management throughout the regeneration process. Therefore, a carbon adsorber is needed to remove hydrocarbon presence and the carbon block itself must be protected from particles ingression.
Parker’s XtreamSorb combines a particulate filtration and carbon adsorption in a single unique device. By combining multiple filtration and separation technologies into one system, customers can benefit from increased efficiency, and reduced complexity, cost, and footprint. Proprietary carbon block technology ensures higher adsorption and no release of carbon fines.
After the desorber, the lean amine is looped back to the top of the solvent contact tower (absorber) and simple particulate filtration with XtreamPure will ensure no solids are carried over from the piping and equipment network to maintain absorption efficiency.
Related products:
OUTLET GAS COALESCING
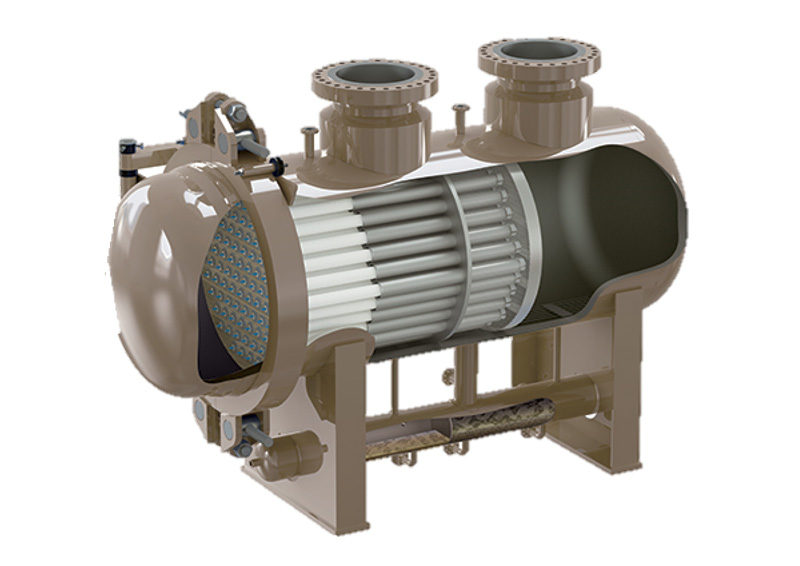
To protect the compressor before storage, the carbon dioxide stripped by the desorber must be filtered to remove particulate and coalesced to remove moisture.
The Gemini Gas Coalescer incorporating PEACH coalescing technology has been proven in the Oil and Gas market for many years - delivering superior performance in a trouble-free design. By combining multiple filtration and separation technologies into one system, customers can benefit from increased efficiency, reduced complexity, cost and reduced footprint.
Related product:
FLUID CONVEYANCE FOR BLUE HYDROGEN PRODUCTION
The use of fluid conveyance technology in carbon capture and storage (CCS)
Fluid conveyance products such as pipe systems, valves and fittings play an essential role in Hydrogen carbon capture and storage (CCS) applications. Parker’s products are well placed to handle the pressures and temperatures required for CCS and are made of materials that are compatible with the fluids and chemicals used in the process.
Featured fittings, needle, ball, check and modular system valve products
In CCS applications, Parker’s products are used to transport hydrogen and carbon dioxide between the capture, transportation, and storage stages. The products are designed to handle the unique properties of hydrogen and carbon dioxide. As hydrogen is a highly reactive gas that can cause embrittlement and cracking in certain metals, Parker has developed a range of solutions for hydrogen CCS applications that are manufactured from corrosion resistant alloys and are compatible with hydrogen.


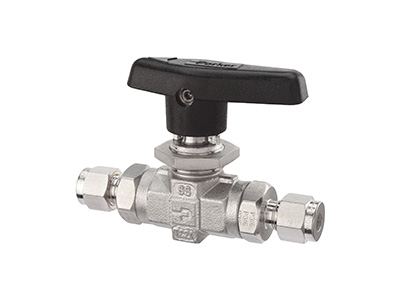
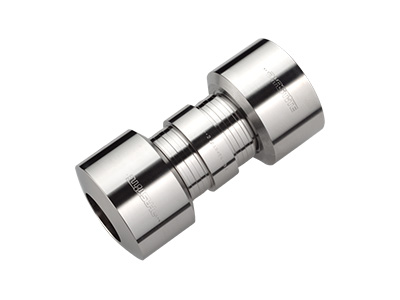
Related products:
- Two Ferrule Tube Fittings A-LOK®
- Single Ferrule Tube Fittings CPI™
- Permanent Tube Fittings Phastite®
- Medium Pressure Needle Valves Parker Autoclave
- MPI Needle Valves MAN Series
- Medium Pressure Check Valves Parker Autoclave
- Isolation Ball Valves Hi-Pro Series
- Ball Valves B Series
- Ball Valves, Trunnion Style, HB Series
- Modular Sample Conditioning System IntraFlow™